Catenary detection and maintenance vehicle and method based on lidar
A technology of laser radar and catenary, applied in the direction of overhead lines, etc., can solve the problems of fatigue and slackness of operators, low detection efficiency, large error of detection results, etc.
- Summary
- Abstract
- Description
- Claims
- Application Information
AI Technical Summary
Problems solved by technology
Method used
Image
Examples
Embodiment 1
[0071] Such as Figure 1-3 As shown, a lidar-based catenary detection and maintenance vehicle provided in this embodiment includes a detection vehicle body 1, a data acquisition unit, a lifting and rotating work platform 3 and a server 4 for data analysis and processing; the data acquisition unit includes The lidar sensor 2 that is arranged on the front of the roof of the detection car body 1; the detection car body 1 travels on the track 6, the laser radar sensor 2 is provided with a laser automatic scanner, and the scanning direction of the laser automatic scanner is aligned with the vehicle to be detected. Catenary 8. 9 of them are columns.
[0072] The lifting and rotating operation platform 3 can be lifted and rotated and arranged behind the top of the detection vehicle body 1; the lifting and rotating operation platform 3 is provided with a display and control panel (not shown); the server 4 communicates with the data acquisition unit in a wired manner and through wirel...
Embodiment 2
[0082] A catenary geometric parameter detection method based on the lidar sensor, the steps are:
[0083] (1) Using a single-line laser radar to scan, obtain a plurality of continuous scan data within the scan range and convert the scan data into space Cartesian coordinate system data;
[0084] (2) Sorting the spatial Cartesian coordinate system data in chronological order or displacement order, selecting data whose guide height and pull-out value are within a preset range, to obtain valid data for detection;
[0085] The preset range of pull-out value is -600mm~600mm. When it is a high-speed railway, the preset range of guide height is 5000mm~5800mm; when it is a normal speed railway, the preset range of guide height is 5800mm~6600mm; , The preset range of guide height is 3600mm~4400mm.
[0086] (3) Find the data point corresponding to the minimum conductance value in each row of data of the effective data, and obtain the contact position of the pantograph and contact wire w...
Embodiment 3
[0095] Such as Figure 5 As shown, a lidar-based catenary detection and maintenance method, the steps include:
[0096] (1) Data acquisition: the laser radar sensor scans the catenary, the pillar positioning unit collects the number information of the detected catenary pillar, and the inclination sensor measures the inclination angle of the detected vehicle body; the data acquisition unit transmits the collected data to said server;
[0097] (2) Differentiate data: the server distinguishes the received data and identifies different data types;
[0098] (3) Data processing: the server determines the detected catenary pillar number according to the data collected by the pillar positioning unit; the server calculates the geometric parameter value of the detected catenary according to the information collected by the laser radar sensor and the inclination sensor;
[0099] (4) Data comparison: the server compares the measured catenary geometric parameter value with the preset val...
PUM
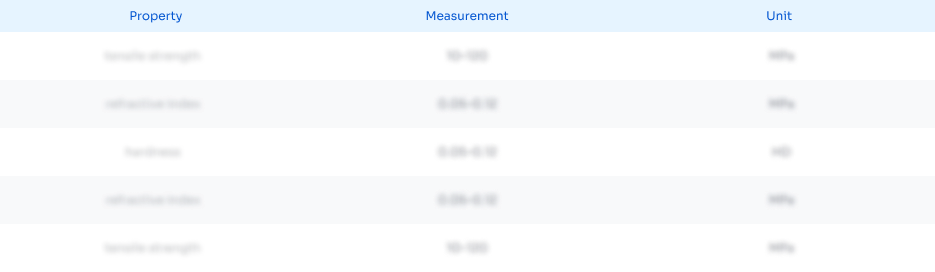
Abstract
Description
Claims
Application Information

- R&D
- Intellectual Property
- Life Sciences
- Materials
- Tech Scout
- Unparalleled Data Quality
- Higher Quality Content
- 60% Fewer Hallucinations
Browse by: Latest US Patents, China's latest patents, Technical Efficacy Thesaurus, Application Domain, Technology Topic, Popular Technical Reports.
© 2025 PatSnap. All rights reserved.Legal|Privacy policy|Modern Slavery Act Transparency Statement|Sitemap|About US| Contact US: help@patsnap.com