Precise composite molding grinding machine for numerical control linear guide rail
A compound molding and linear guide rail technology, which is applied in the direction of grinding machines, grinding bed, portal grinding machine tools, etc., can solve the problem of motion distortion accuracy affecting the motion distortion accuracy of linear guide rail, large center distance between vertical and horizontal grinding heads, structural influence, etc. problems, to achieve the effect of improving processing efficiency, improving grinding accuracy and reducing impact
- Summary
- Abstract
- Description
- Claims
- Application Information
AI Technical Summary
Problems solved by technology
Method used
Image
Examples
Embodiment Construction
[0013] refer to Figure 1 to Figure 3 , a numerically controlled linear guide rail precision compound molding grinding machine of the present invention, comprising a U-shaped base 1, on which an embedded grinding table 2 driven by a driving device and capable of longitudinal and horizontal movement is arranged, the A magnetic fixture 3 for fixing the guide rail is installed on the embedded grinding table 2, a gantry 4 is arranged above the U-shaped base 1, and the first and second transverse drive mechanisms 5 and 6 are installed on the gantry beam respectively, and the second 1. The first and second vertical grinding head mechanisms 9 and 10 are installed on the second transverse drive mechanism 5 and 6 respectively through the first and second vertical drive mechanisms 7 and 8, and the front of the gantry 4 is provided with a vertical Type supporting frame 11, the third horizontal driving mechanism 12 is installed on this vertical supporting frame 11, and the third horizonta...
PUM
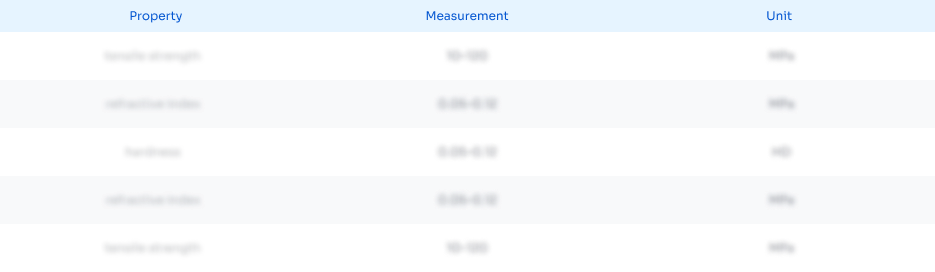
Abstract
Description
Claims
Application Information

- Generate Ideas
- Intellectual Property
- Life Sciences
- Materials
- Tech Scout
- Unparalleled Data Quality
- Higher Quality Content
- 60% Fewer Hallucinations
Browse by: Latest US Patents, China's latest patents, Technical Efficacy Thesaurus, Application Domain, Technology Topic, Popular Technical Reports.
© 2025 PatSnap. All rights reserved.Legal|Privacy policy|Modern Slavery Act Transparency Statement|Sitemap|About US| Contact US: help@patsnap.com