2, 3-dichloropyridine preparation method
A technology of dichloropyridine and dicarboxamide pyridine, which is applied in the field of preparing 2,3-dichloropyridine, can solve the problems of high toxicity of dichloromethane, potential safety hazards, and difficulty in recycling, and achieve low production cost and high product yield. Efficiency and quality, stable and safe response
- Summary
- Abstract
- Description
- Claims
- Application Information
AI Technical Summary
Problems solved by technology
Method used
Examples
Embodiment 1
[0025] (1) Keep the temperature at 5-20℃, add 330kg of 2,3-dimethylamide pyridine to 1320kg of purified water, stir until the 2,3-dimethylamide pyridine is completely dissolved, and then add 30% mass fraction dropwise successively 533.3kg of sodium hydroxide aqueous solution and 3132.6kg of sodium hypochlorite aqueous solution with a mass fraction of 9.5%. The temperature and stirring conditions of 5~20℃ are maintained during the dripping process. The dripping time is controlled within 3h. After the dripping is completed, the temperature is raised to 80~100℃, keep stirring for 2h to make the reaction fully proceed. After the reaction is completed, add hydrochloric acid to adjust the pH of the system to 7 to remove excess sodium hydroxide, and distill under reduced pressure to remove the water in the system to obtain 2,3-di Crude aminopyridine.
[0026] (2) Add the crude 2,3-diaminopyridine obtained in step (1) to 1944.5 kg of hydrochloric acid with a mass fraction of 30%, and add...
Embodiment 2
[0029] (1) Keep the temperature at 5-20℃, add 330kg of 2,3-dimethylamide pyridine to 1980kg purified water, stir until the 2,3-dimethylamide pyridine is completely dissolved, and then dropwise add 46% mass fraction successively 609.8kg of potassium hydroxide aqueous solution and 3234.8kg of sodium hypochlorite aqueous solution with a mass fraction of 11.5%. The temperature and stirring conditions of 5~20℃ are maintained during the dripping process. The dripping time is controlled within 3h. After the dripping is completed, the temperature is raised to 80~100℃, keep for 2h under stirring to make the reaction fully proceed. After the reaction is completed, add hydrochloric acid to adjust the pH of the system to 5-6 to remove excess sodium hydroxide, and distill under reduced pressure to remove the water in the system to obtain 2,3 -Crude diaminopyridine.
[0030] (2) Add the crude 2,3-diaminopyridine obtained in step (1) to 2878.4 kg of hydrochloric acid with a mass fraction of 38%...
Embodiment 3
[0033] (1) Keep the temperature at 5-20℃, add 330kg of 2,3-dimethylamide pyridine to 1320kg of purified water, stir until the 2,3-dimethylamide pyridine is completely dissolved, and then dropwise add 35% mass fraction successively 457.1kg of sodium hydroxide aqueous solution and 2834.3kg of sodium hypochlorite aqueous solution with a mass fraction of 10.5%. The temperature and stirring conditions of 5-20℃ are maintained during the dripping process. The dripping time is controlled within 3h. After the dripping is completed, the temperature is raised to 80~100℃, keep for 2h under stirring to make the reaction fully proceed. After the reaction is completed, add hydrochloric acid to adjust the pH of the system to 4~5 to remove excess sodium hydroxide, and distill under reduced pressure to remove the water in the system to obtain 2,3 -Crude diaminopyridine.
[0034] (2) Add the crude 2,3-diaminopyridine obtained in step (1) to 1767.8 kg of hydrochloric acid with a mass fraction of 33%...
PUM
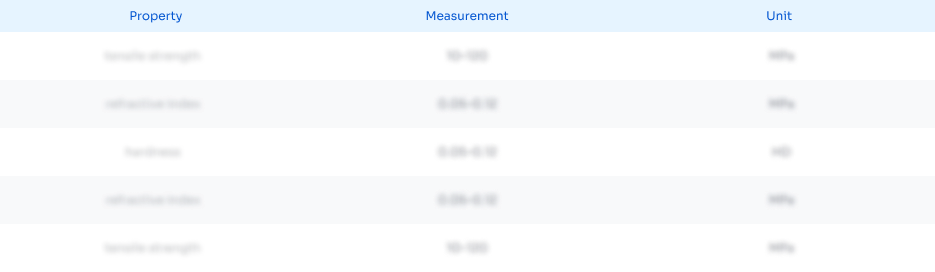
Abstract
Description
Claims
Application Information

- R&D
- Intellectual Property
- Life Sciences
- Materials
- Tech Scout
- Unparalleled Data Quality
- Higher Quality Content
- 60% Fewer Hallucinations
Browse by: Latest US Patents, China's latest patents, Technical Efficacy Thesaurus, Application Domain, Technology Topic, Popular Technical Reports.
© 2025 PatSnap. All rights reserved.Legal|Privacy policy|Modern Slavery Act Transparency Statement|Sitemap|About US| Contact US: help@patsnap.com