Sulfur Recovery Process with Low Sulfur Emissions
A technology of sulfur recovery and sulfur discharge, which is applied in the direction of sulfur preparation/purification, sulfur compounds, inorganic chemistry, etc., and can solve problems such as polluted environment, limited facilities, and environmental pollution
- Summary
- Abstract
- Description
- Claims
- Application Information
AI Technical Summary
Problems solved by technology
Method used
Image
Examples
Embodiment 1
[0054] A set of 50,000 tons / year sulfur recovery unit in the refinery, including sequentially connected combustion furnace, primary Claus reactor, secondary Claus reactor, selective hydrogenation reduction reactor, selective oxidation reaction device and two adsorption desulfurization towers that can be connected in series and parallel, and the upper part of the first-stage Claus reactor is filled with Fe 2 o 3 / Al 2 O deoxidation protection type sulfur recovery catalyst 15m 3 , the lower part is filled with TiO 2 Sulfur recovery catalyst 25m 3 ; The upper part of the secondary Claus reactor is filled with Fe 2 o 3 / Al 2 o 3 Deoxidation protection type sulfur recovery catalyst 15m 3 , the lower part is filled with TiO 2 / Al 2 o 3 Sulfur recovery catalyst 25m 3 ; Selective hydrogenation reduction reactor filled with CoO-MoO 3 / Al 2 o 3 Selective reduction of SO 2 Catalyst 20m 3 , the selective oxidation reactor is filled with Fe 2 o 3 / SiO 2 selective oxidat...
Embodiment 2
[0069] A 30,000-ton / year sulfur recovery unit in a methanol plant, including sequentially connected combustion furnaces, primary Claus reactors, secondary Claus reactors, selective hydrogenation reduction reactors, selective oxidation reactions device and two adsorption desulfurization towers that can be connected in series and parallel, and the upper part of the first-stage Claus reactor is filled with Fe 2 o 3 / Al 2 O deoxidation protection type sulfur recovery catalyst 12m 3 , the lower part is filled with TiO 2 Sulfur recovery catalyst 20m 3 ; The upper part of the secondary Claus reactor is filled with Fe 2 o 3 / Al 2 o 3 Deoxidation protection type sulfur recovery catalyst 12m 3 , the lower part is filled with TiO 2 Sulfur recovery catalyst 20m 3 ; Selective hydrogenation reduction reactor filled with CoO-MoO 3 / Al 2 o 3 Selective reduction of SO 2 Catalyst 15m 3 , the selective oxidation reactor is filled with Fe 2 o 3 / SiO 2 selective oxidation of H 2...
PUM
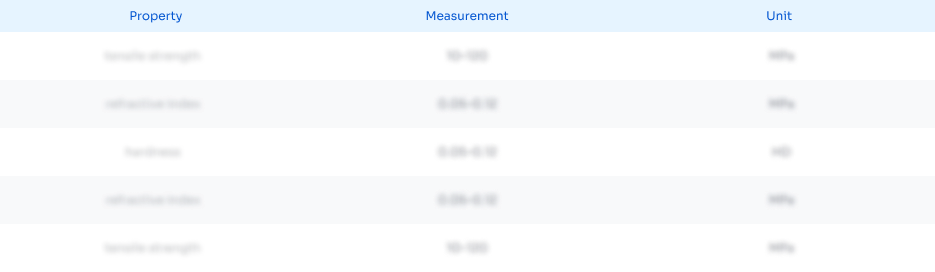
Abstract
Description
Claims
Application Information

- Generate Ideas
- Intellectual Property
- Life Sciences
- Materials
- Tech Scout
- Unparalleled Data Quality
- Higher Quality Content
- 60% Fewer Hallucinations
Browse by: Latest US Patents, China's latest patents, Technical Efficacy Thesaurus, Application Domain, Technology Topic, Popular Technical Reports.
© 2025 PatSnap. All rights reserved.Legal|Privacy policy|Modern Slavery Act Transparency Statement|Sitemap|About US| Contact US: help@patsnap.com