Industrial robot operator working from multiple angles
An industrial robot and operator technology, applied in the field of machinery, can solve the problems of high maintenance cost, high cost of hydraulic components, and insufficient response, and achieve the effect of large working space, good force, and easy remote control
- Summary
- Abstract
- Description
- Claims
- Application Information
AI Technical Summary
Problems solved by technology
Method used
Image
Examples
Embodiment 1
[0017] Industrial robot manipulator for multi-angle work, including rod one 11, rod two 12, rod three 13, telescopic rod one 31, telescopic rod two 32, sliding sleeve one 21, sliding sleeve two 22, sliding sleeve three 23, slider 24 , actuator 25 and working platform 26,
[0018] The lower end of the telescopic rod one 31 is connected to the slide block 24 through the rotary pair one 1, and the slide block 24 is installed in the chute on the working platform 26, and the upper end of the telescopic rod one 31 is connected with one end of the rod two 12 through the rotary pair two 2, and the rod two The other end of the second 12 is connected to the actuator 25 through the rotating pair three 3,
[0019] The lower end of rod one 11 is connected on the working platform 26 through the rotating pair four 4, the upper end of rod one 11 is connected on the sliding sleeve three 23 through the rotating pair five 5, and the sliding sleeve three 23 is sleeved on the rod two 12,
[0020]...
PUM
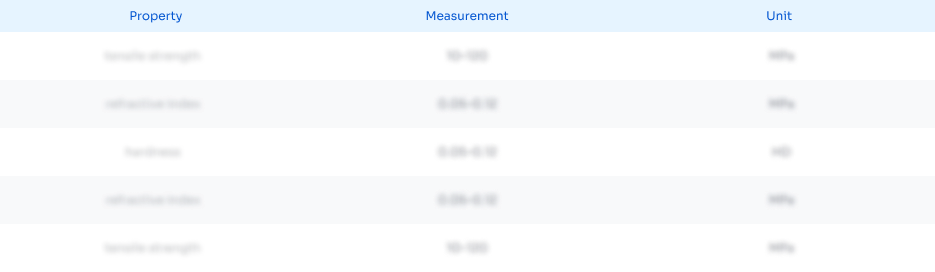
Abstract
Description
Claims
Application Information

- Generate Ideas
- Intellectual Property
- Life Sciences
- Materials
- Tech Scout
- Unparalleled Data Quality
- Higher Quality Content
- 60% Fewer Hallucinations
Browse by: Latest US Patents, China's latest patents, Technical Efficacy Thesaurus, Application Domain, Technology Topic, Popular Technical Reports.
© 2025 PatSnap. All rights reserved.Legal|Privacy policy|Modern Slavery Act Transparency Statement|Sitemap|About US| Contact US: help@patsnap.com