Manufacturing method of glass particle stack
A glass particle and manufacturing method technology, applied in glass manufacturing equipment, glass molding, manufacturing tools, etc., can solve the problem of glass particle stack outer diameter change, etc., and achieve the effect of preventing interface irregularities
- Summary
- Abstract
- Description
- Claims
- Application Information
AI Technical Summary
Problems solved by technology
Method used
Image
Examples
Embodiment 1
[0028] The number of interference layers from the rod interface (one layer is stacked in one reciprocation movement) was changed, and the glass fine particle stacks 5 were each produced by the production method according to the embodiment of the present invention. Then, the presence or absence of interface irregularities and the presence or absence of unsintered portions were investigated for each of the manufactured glass fine particle stacks 5 . express the result in Image 6 , Figure 7 middle. In addition, in Example 1, the ratio of the flow rate of hydrogen gas which will be described later was set to 1.17.
[0029] Image 6 It is a graph showing the relationship between the ratio of the interference layer to the total number of laminations per glass particle stack and the incidence of interface irregularities. according to Image 6It can be seen that when the ratio of the interference layer to the total number of laminations is about 0.2% or more, there is an effect...
Embodiment 2
[0032] The bulk density of the glass particle stack is proportional to the flow rate of the combustible gas in the nozzle, so the flow rate of the combustible gas, that is, hydrogen gas (hydrogen and oxygen gas is used in the flame formation of the nozzle in this embodiment) was changed, and the investigation The occurrence rate of interface irregularities due to the difference in packing density of the interference layer. When the number of layers of the interference layer from the rod interface is set constant (3 layers), and the flow rate of the hydrogen gas in the nozzles 4a to 4g is changed when forming the interference layer, and using the production method according to the embodiment of the present invention, respectively Production of the glass fine particle stacked body 5 is performed. Then, the presence or absence of interface irregularities was investigated for each of the produced glass fine particle stacks 5 . Figure 8 is the ratio of the flow rate of hydrogen g...
PUM
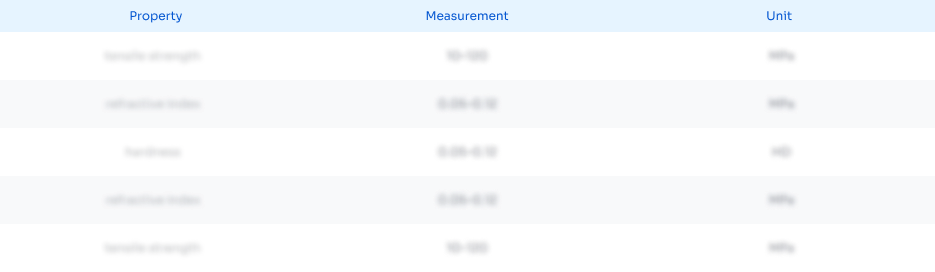
Abstract
Description
Claims
Application Information

- R&D Engineer
- R&D Manager
- IP Professional
- Industry Leading Data Capabilities
- Powerful AI technology
- Patent DNA Extraction
Browse by: Latest US Patents, China's latest patents, Technical Efficacy Thesaurus, Application Domain, Technology Topic, Popular Technical Reports.
© 2024 PatSnap. All rights reserved.Legal|Privacy policy|Modern Slavery Act Transparency Statement|Sitemap|About US| Contact US: help@patsnap.com