A three-dimensional braided composite power transmission tower and its preparation method
A technology of transmission poles and towers and three-dimensional weaving, which is applied in chemical instruments and methods, towers, building types, etc., can solve problems such as hidden dangers of structural defects and achieve the effect of improving mechanical properties
- Summary
- Abstract
- Description
- Claims
- Application Information
AI Technical Summary
Problems solved by technology
Method used
Image
Examples
Embodiment 1
[0037] Preparation of cross-arm and support rods at tower head: T300 carbon fiber is used as zero-degree yarn to prepare carbon fiber center zero-degree yarn skeleton 1 for cross-arm and support rods. 6% of the cross-sectional radius of the rod part. After the zero-degree yarn is prepared, the three-dimensional fabric core structure is woven with a three-dimensional five-way process on the basis of the carbon fiber yarn skeleton. For the material, the entire weaving thickness accounts for 75% of the cross-sectional radius of the cross-arm and support rod parts of the tower. After the core glass fiber three-dimensional fabric is woven, the yarn type is adjusted and T700 carbon fiber is introduced. The proportion of carbon fiber in the mixed yarn is 93%, the three-dimensional four-way weaving structure is selected for the outer three-dimensional fabric processing, and the thickness of the obtained hybrid fiber fabric transition layer 3 accounts for 19% of the radius of the rod bo...
Embodiment 2
[0043] Preparation of cross-arm and support rods at tower head: T300 carbon fiber is used as zero-degree yarn to prepare carbon fiber center zero-degree yarn skeleton 1 for cross-arm and support rods. 7% of the cross-sectional radius of the rod part. After the zero-degree yarn is prepared, the three-dimensional fabric core structure is woven with a three-dimensional five-way process on the basis of the carbon fiber yarn skeleton. The structure of the glass fiber fabric 2 in the core is woven with high-strength S glass For the material, the entire weaving thickness accounts for 74% of the cross-sectional radius of the cross-arm and support rod parts of the tower. After the core glass fiber three-dimensional fabric is woven, the yarn type is adjusted and T300 carbon fiber is introduced. The proportion of carbon fiber in the mixed yarn is 92%, the three-dimensional four-way weaving structure is selected for the outer layer three-dimensional fabric processing, and the thickness of ...
Embodiment 3
[0049] Preparation of cross-arm and support rods at tower head: T300 carbon fiber is used as zero-degree yarn to prepare carbon fiber center zero-degree yarn skeleton 1 for cross-arm and support rods. 9% of the cross-sectional radius of the rod part. After the zero-degree yarn is prepared, the three-dimensional fabric core structure is woven with a three-dimensional four-way process on the basis of the carbon fiber yarn skeleton. The structure of the glass fiber fabric 2 in the core is woven with high-strength S glass For the material, the entire weaving thickness accounts for 70% of the cross-sectional radius of the cross-arm and support rod parts of the tower. After the core glass fiber three-dimensional fabric is woven, the yarn type is adjusted and T800 carbon fiber is introduced. The proportion of carbon fiber in the mixed yarn is 91%, the three-dimensional four-way weaving structure is selected to process the three-dimensional fabric of the outer layer, and the thickness ...
PUM
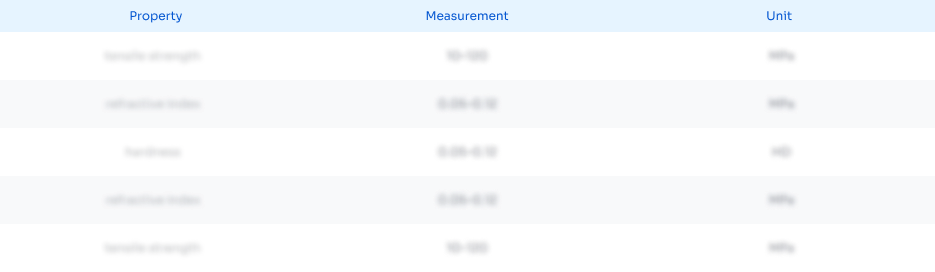
Abstract
Description
Claims
Application Information

- R&D
- Intellectual Property
- Life Sciences
- Materials
- Tech Scout
- Unparalleled Data Quality
- Higher Quality Content
- 60% Fewer Hallucinations
Browse by: Latest US Patents, China's latest patents, Technical Efficacy Thesaurus, Application Domain, Technology Topic, Popular Technical Reports.
© 2025 PatSnap. All rights reserved.Legal|Privacy policy|Modern Slavery Act Transparency Statement|Sitemap|About US| Contact US: help@patsnap.com