Method for producing by-product cyclohexanone-oxime through flue gas desulphurization by ammonia method
A technology of cyclohexanone oxime and flue gas, which is applied in the preparation of cyclohexanone oxime and the field of cyclohexanone oxime by-product of ammonia flue gas desulfurization, can solve the problems of poor economy and large consumption, and achieve large product sales, High added value and the effect of improving economic benefits
- Summary
- Abstract
- Description
- Claims
- Application Information
AI Technical Summary
Problems solved by technology
Method used
Image
Examples
preparation example Construction
[0019] The preparation method of the present invention is basically realized through the following steps (see attached figure 1 ):
[0020] Step A Ammonia flue gas desulfurization to prepare ammonium bisulfite: use ammonia or ammonia water as absorbent to absorb sulfur dioxide in the flue gas to prepare ammonium bisulfite. The concentration of ammonia in the absorbent is 5-100 wt%, preferably 25-33 wt%.
[0021] Step B: solid-liquid separation of desulfurization absorption liquid: removal of solid impurities in the ammonium bisulfite solution, which is a preferred step.
[0022] Preparation of step C hydroxylamine sulfate: react ammonium bisulfite with nitrite and sulfur dioxide to prepare hydroxylamine sulfate.
[0023] Step D dehydrates and concentrates the hydroxylamine sulfate solution prepared in step C, which is a preferred step.
[0024] Step E oximation of cyclohexanone: reaction of hydroxylamine sulfate and cyclohexanone by countercurrent oximation to prepare cyclo...
Embodiment 1
[0071] The treatment object is: 220t / h power plant boiler flue gas, of which SO 2 Content 500mg / Nm 3 , with the concentration of 28wt% ammonia as absorbent.
[0072] The specific steps are: the flue gas enters the absorption tower with a flow rate of 270000Nm 3 / h, absorbed by a two-stage absorption tower. The flow rate of fresh ammonia water added during the absorption process is 0.17m 3 / h. In the first-stage absorption tower, add an oxygen inhibitor, such as p-phenylenediamine, to the absorption liquid, and control the absorption temperature at 40°C; in the second-stage absorption tower, control the absorption temperature at 25°C, and the pH of the liquid in the tower 5.0-5.5. Obtaining the concentration of ammonium bisulfite solution product from the bottom of the primary absorption tower is 32.8kg / m 3 , and containing ammonium sulfite 1.4kg / m 3 . SO in the tail gas discharged from the secondary absorption tower 2 The content is 3.6mg / m 3 , Ammonia escape amount ...
Embodiment 2
[0076] The treatment object is: 220t / h power plant boiler flue gas, of which SO 2 Content 2000mg / Nm 3 , with the concentration of 28wt% ammonia as absorbent.
[0077] The specific steps are: the flue gas enters the absorption tower with a flow rate of 270000Nm 3 / h, absorbed by a two-stage absorption tower. The flow rate of fresh ammonia water added during the absorption process is 0.68m 3 / h. In the first-stage absorption tower, add an oxygen inhibitor, such as p-phenylenediamine, to the absorption liquid, and control the absorption temperature at 40°C; in the second-stage absorption tower, control the absorption temperature at 25°C, and the pH of the liquid in the tower 5.0-5.5; the tail gas is discharged after being washed with water and defogged. SO in exhaust gas 2 Content less than 100mg / m 3 , the amount of ammonia escape is less than 5mg / m 3 . Obtaining the concentration of ammonium bisulfite solution product from the bottom of the primary absorption tower is 1...
PUM
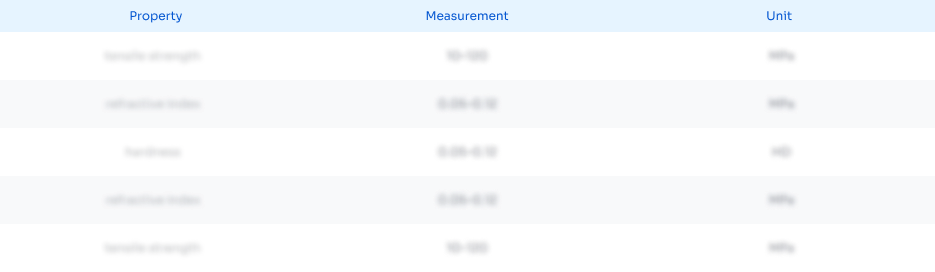
Abstract
Description
Claims
Application Information

- Generate Ideas
- Intellectual Property
- Life Sciences
- Materials
- Tech Scout
- Unparalleled Data Quality
- Higher Quality Content
- 60% Fewer Hallucinations
Browse by: Latest US Patents, China's latest patents, Technical Efficacy Thesaurus, Application Domain, Technology Topic, Popular Technical Reports.
© 2025 PatSnap. All rights reserved.Legal|Privacy policy|Modern Slavery Act Transparency Statement|Sitemap|About US| Contact US: help@patsnap.com