Preparing method of high purity quartz sleeve for large-size optical fiber preform
An optical fiber preform, quartz sleeve technology, applied in glass manufacturing equipment, manufacturing tools, glass molding and other directions, can solve the problems of inability to effectively increase the size of powder rods, radial density cracking or fracture, etc., to ensure density consistency , the effect of improving resilience and wide application prospects
- Summary
- Abstract
- Description
- Claims
- Application Information
AI Technical Summary
Problems solved by technology
Method used
Image
Examples
Embodiment 1
[0039] Example 1: Manufacturing a Φ300mm×2000mm optical fiber preform with a quartz sleeve
[0040] (1) The target rod made of quartz glass is pickled, soaked in hydrochloric acid with a concentration of 5% for 1 hour to remove impurities attached to the surface of the target rod, then rinsed repeatedly with deionized water, and finally dried.
[0041] (2) Place the pretreated target rod vertically in the upper and lower chucks of the deposition machine, adjust the position and lock it, and rotate the target rod at 20rpm. Decamethylcyclopentasiloxane, oxygen, hydrogen, and nitrogen are used as raw material gases to feed the blowtorch, and the flow rates are 20g / min, 20L / min, 40L / min, and 10L / min to ignite the blowtorch gas. Choose one blowtorch made of quartz material for each group, and the three groups of blowtorches longitudinally deposit back and forth in the corresponding E, M, and S ranges. The axial travel speed of the blowtorch is 100mm / min, and the pressure in the rea...
Embodiment 2
[0044] Example 2: Manufacture of a quartz sleeve for an optical fiber preform of Φ300mm×2500mm
[0045] (1) The target tube made of quartz glass is pickled, soaked in 10% nitric acid for 1.5 hours to remove impurities attached to the surface of the target tube, then rinsed repeatedly with deionized water, and finally dried.
[0046] (2) Place the pretreated target tube vertically in the upper and lower chucks of the deposition machine, adjust the position and lock it, and rotate the target rod at 35rpm. Use octamethylcyclotetrasiloxane, oxygen, natural gas, and nitrogen as raw material gases to feed the blowtorch, and the flow rates are 20g / min, 40L / min, 70L / min, and 15L / min to ignite the blowtorch gas. Choose one metal blowtorch for each group, 3 groups of blowtorches are longitudinally deposited back and forth in the corresponding E, M, S ranges, the axial travel speed of the blowtorch is 200mm / min, and the pressure in the reaction chamber is maintained at -40pa. During the...
Embodiment 3
[0049] Example 3: Manufacture of a quartz sleeve for an optical fiber preform of Φ360mm×2500mm
[0050] (1) The target tube made of quartz glass is pickled, soaked in sulfuric acid with a concentration of 15% for 2 hours to remove impurities attached to the surface of the target tube, then rinsed repeatedly with deionized water, and finally dried.
[0051] (2) Place the pretreated target tube vertically in the upper and lower chucks of the deposition machine, adjust the position and lock it, and rotate the target rod at 50rpm. Hexamethylcyclotrisiloxane, oxygen, methane, and nitrogen are used as raw material gases to pass into the torch, and the flow rates are 20g / min, 60L / min, 100L / min, and 20L / min to ignite the torch gas. Each group of 2 metal blowtorches is selected, and the 3 groups of blowtorches are longitudinally deposited back and forth in the corresponding E, M, and S ranges. The axial travel speed of the blowtorches is 300mm / min, and the pressure in the reaction cham...
PUM
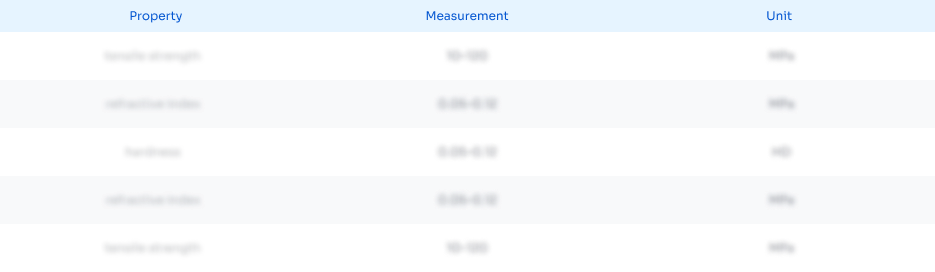
Abstract
Description
Claims
Application Information

- R&D
- Intellectual Property
- Life Sciences
- Materials
- Tech Scout
- Unparalleled Data Quality
- Higher Quality Content
- 60% Fewer Hallucinations
Browse by: Latest US Patents, China's latest patents, Technical Efficacy Thesaurus, Application Domain, Technology Topic, Popular Technical Reports.
© 2025 PatSnap. All rights reserved.Legal|Privacy policy|Modern Slavery Act Transparency Statement|Sitemap|About US| Contact US: help@patsnap.com