Cable
A cable and cable technology, applied in the direction of insulated cables, cables, circuits, etc., can solve the problems of easy aging, shorten the service life of cables, low tensile strength, etc. The effect of increasing tensile strength
- Summary
- Abstract
- Description
- Claims
- Application Information
AI Technical Summary
Problems solved by technology
Method used
Image
Examples
Embodiment 1
[0038] 100 parts of iron, 500 parts of manganese, 80 parts of silicon, 20 parts of carbon, 20 parts of titanium carbide, 20 parts of molybdenum, 10 parts of scandium, 5 parts of lanthanum, through the following steps to make ferromanganese alloy:
[0039] S1. Sieve the iron powder so that the particle size of the iron powder is between 200-400 mesh, and sieve the manganese powder so that the particle size of the manganese powder is between 300-400 mesh;
[0040] S2. Put the iron powder, manganese powder and other ingredients that meet the requirements into the ball mill for 2-3 hours and then let it stand for 1 hour;
[0041] S3, vacuum drying;
[0042] S4, sieving;
[0043] S5, 500 degree vacuum sintering for 1 hour, 800 degree vacuum sintering for half an hour, 1100 degree vacuum sintering for half an hour, and 1400 degree vacuum sintering for 2 hours.
[0044]Iron and manganese are the main components of ferromanganese alloy. Too little iron powder will reduce the strengt...
Embodiment 2
[0046] 300 parts of iron, 200 parts of manganese, 50 parts of silicon, 30 parts of carbon, 30 parts of titanium carbide, 10 parts of molybdenum, 5 parts of scandium, 10 parts of lanthanum, through the following steps to make ferromanganese alloy:
[0047] S1. Sieve the iron powder so that the particle size of the iron powder is between 200-400 mesh, and sieve the manganese powder so that the particle size of the manganese powder is between 300-400 mesh;
[0048] S2. Put the iron powder, manganese powder and other ingredients that meet the requirements into the ball mill for 2-3 hours and then let it stand for 1 hour;
[0049] S3, vacuum drying;
[0050] S4, sieving;
[0051] S5, 700 degree vacuum sintering for 1 hour, 1000 degree vacuum sintering for half an hour, 1300 degree vacuum sintering for half an hour, and 1500 degree vacuum sintering for 2 hours.
Embodiment 3
[0053] 200 parts of iron, 400 parts of manganese, 60 parts of silicon, 25 parts of carbon, 25 parts of titanium carbide, 15 parts of molybdenum, 7 parts of scandium, 8 parts of lanthanum, through the following steps to make ferromanganese alloy:
[0054] S1. Sieve the iron powder so that the particle size of the iron powder is between 200-400 mesh, and sieve the manganese powder so that the particle size of the manganese powder is between 300-400 mesh;
[0055] S2. Put the iron powder, manganese powder and other ingredients that meet the requirements into the ball mill for 2-3 hours and then let it stand for 1 hour;
[0056] S3, vacuum drying;
[0057] S4, sieving;
[0058] S5, 600 degree vacuum sintering for 1 hour, 900 degree vacuum sintering for half an hour, 1200 degree vacuum sintering for half an hour, and 1450 degree vacuum sintering for 2 hours.
PUM
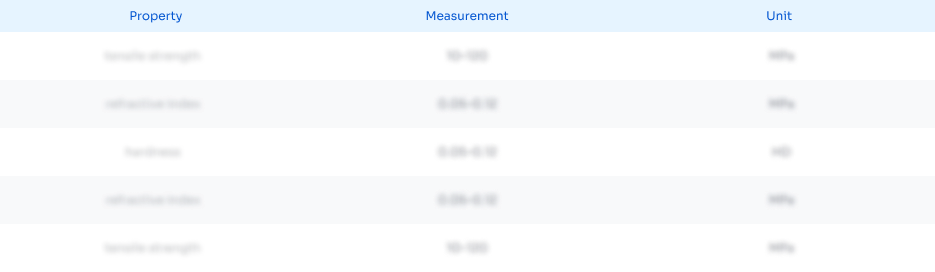
Abstract
Description
Claims
Application Information

- Generate Ideas
- Intellectual Property
- Life Sciences
- Materials
- Tech Scout
- Unparalleled Data Quality
- Higher Quality Content
- 60% Fewer Hallucinations
Browse by: Latest US Patents, China's latest patents, Technical Efficacy Thesaurus, Application Domain, Technology Topic, Popular Technical Reports.
© 2025 PatSnap. All rights reserved.Legal|Privacy policy|Modern Slavery Act Transparency Statement|Sitemap|About US| Contact US: help@patsnap.com