Waterproof and ultraviolet-proof safety rope coating
An anti-ultraviolet and rope technology, which is applied in textiles, papermaking, fiber treatment, etc., can solve problems such as the firmness of graphene coatings that do not consider waterproof performance, and achieve good water resistance, easy-to-use process formulas, and simple process formulas Effect
- Summary
- Abstract
- Description
- Claims
- Application Information
AI Technical Summary
Problems solved by technology
Method used
Image
Examples
Embodiment 1
[0016] It consists of the following components in parts by weight: 15% polyurethane, 10% water-based silicone waterproofing agent, 1% polytetrafluoroethylene, 2[2'-hydroxy-4'(α-methacryloyloxy)phenyl ]-2-benzotriazole 3%, graphene 5%, carboxymethyl cellulose 5%, defoamer 3-iodo-2-propynyl butyl carbamate 1%, silane coupling agent 0.05% of 3-aminopropyltriethoxysilane, 0.05% of emulsifier Span-400, 0.05% of zinc naphthenate as a drier, 1% of butyl glycol ether, and the balance is water.
[0017] Its preparation process steps: (1) 15% of the polyurethane, 10% of water-based silicone waterproofing agent, 1% of polytetrafluoroethylene, 2[2'-hydroxyl-4'(α -Methacryloyloxy)phenyl]-2-benzotriazole 3%, graphene 5%, carboxymethyl cellulose 5%, defoamer 3-iodo-2-propynylbutylaminomethyl Ester 1%, silane coupling agent 3-aminopropyltriethoxysilane 0.05%, emulsifier Span-400.05%, drier zinc naphthenate 0.05%, ethylene glycol butyl ether 1%, the rest Water is added into the mixer to vibr...
Embodiment 2
[0019] It consists of the following components in parts by weight: 25% polyurethane, 15% water-based silicone waterproofing agent, 5% polytetrafluoroethylene, 2[2'-hydroxy-4'(α-methacryloyloxy)phenyl ]-2-benzotriazole 5%, graphene 10%, carboxymethyl cellulose 10%, defoamer aniline triethyltrimethoxysilane 5%, silane coupling agent 3-aminopropyl triethyl Oxysilane 0.5%, emulsifier polysorbate-80 1.5%, drier dibutyl dilaurate 0.5%, ethylene glycol butyl ether 5%, and the balance is water.
[0020] Its preparation process steps: (1) 25% of the polyurethane, 15% of water-based silicone waterproofing agent, 5% of polytetrafluoroethylene, 2[2'-hydroxyl-4'(α -Methacryloxy)phenyl]-2-benzotriazole 5%, graphene 10%, carboxymethyl cellulose 10%, defoamer anilinetriethyltrimethoxysilane 5%, silane Joint agent 3-aminopropyltriethoxysilane 0.5%, emulsifier polysorbate-801.5%, drier dibutyl dilaurate 0.5%, ethylene glycol butyl ether 5%, and the rest of water Shake and disperse in the mixe...
Embodiment 3
[0022] It consists of the following components in parts by weight: 21.5% polyurethane, 13.9% water-based silicone waterproofing agent, 2.5% polytetrafluoroethylene, 2[2'-hydroxyl-4'(α-methacryloyloxy)phenyl ]-2-benzotriazole 3.5%, graphene 9.6%, carboxymethyl cellulose 7.8%, defoamer 3-iodo-2-propynyl butyl carbamate 3.2%, silane coupling agent 0.15% of 3-aminopropyltriethoxysilane, 0.95% of emulsifier Span-400, 0.42% of zinc naphthenate as a drier, 4.4% of butyl glycol ether, and the balance is water.
[0023] Its preparation process steps: (1) 21.5% of the polyurethane, 13.9% of water-based silicone waterproofing agent, 2.5% of polytetrafluoroethylene, 3.5% of ultraviolet absorber, 9.6% of graphene, Carboxymethyl cellulose 7.8%, defoamer 3-iodo-2-propynyl butyl carbamate 3.2%, silane coupling agent 0.15%, emulsifier Span-400.95%, drier zinc naphthenate 0.42%, 4.4% ethylene glycol butyl ether, and the rest of water were added to the mixer to oscillate and disperse, the rotat...
PUM
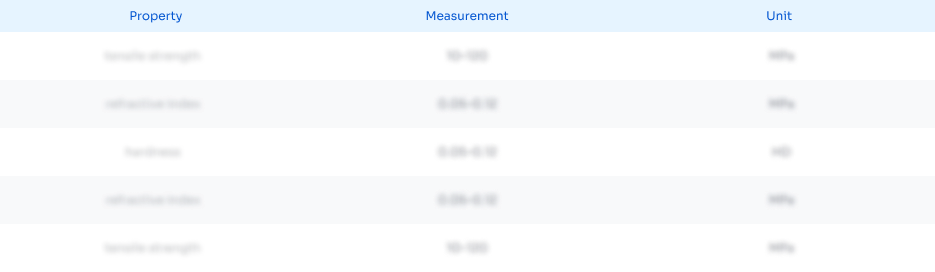
Abstract
Description
Claims
Application Information

- R&D Engineer
- R&D Manager
- IP Professional
- Industry Leading Data Capabilities
- Powerful AI technology
- Patent DNA Extraction
Browse by: Latest US Patents, China's latest patents, Technical Efficacy Thesaurus, Application Domain, Technology Topic, Popular Technical Reports.
© 2024 PatSnap. All rights reserved.Legal|Privacy policy|Modern Slavery Act Transparency Statement|Sitemap|About US| Contact US: help@patsnap.com