A process for improving the scorch performance of neoprene rubber compound
A technology of rubber coke and mixed rubber, which is applied in the field of rubber mixing, can solve the problems of overdue scrapping of mixed rubber materials, economic losses, etc., and achieve the effect of improving scorch performance and ensuring processing safety
- Summary
- Abstract
- Description
- Claims
- Application Information
AI Technical Summary
Problems solved by technology
Method used
Image
Examples
Embodiment 1
[0023] A kind of rubber compound that improves chloroprene rubber scorch performance, and its preferred parts by weight are composed as follows:
[0024] Masterbatch components: 100 parts of neoprene, 1 part of accelerator, 1 part of stearic acid, 2 parts of protective wax, 1 part of antioxidant OCT, 40 parts of fast extrusion carbon black N550, 30 parts of semi-reinforcing carbon black N774 , 20 parts of dioctyl sebacate.
[0025] Small material components: 2 parts of anti-aging agent 3100, 2 parts of anti-aging agent 4010NA, 5 parts of vulcanizing agent. Wherein, the vulcanizing agent is magnesium oxide and zinc oxide or ZIMAG29 / 43.
[0026] A kind of mixing process of the mixed rubber that improves chloroprene rubber scorch performance comprises the following steps:
[0027] (1) Initial mixing: Add 100 parts of neoprene to the internal mixer to press the top bolt, after 30 seconds, raise the top bolt, add 70 parts of carbon black, 20 parts of plasticizer and the remaining...
Embodiment 2
[0030] A kind of rubber compound that improves chloroprene rubber scorch performance, and its preferred parts by weight are composed as follows:
[0031] Masterbatch components: 90 parts of neoprene, 0.5 parts of accelerator, 0.8 parts of stearic acid, 1.5 parts of protective wax, 2.5 parts of antioxidant OCT, 20 parts of fast extrusion carbon black N550, 20 parts of semi-reinforcing carbon black N774 Parts, dioctyl sebacate 15 parts.
[0032] Small material components: 3 parts of anti-aging agent 3100, 1 part of anti-aging agent 4010NA, 9 parts of vulcanizing agent. Wherein, the vulcanizing agent is magnesium oxide and zinc oxide or ZIMAG29 / 43.
[0033] A kind of mixing process of the mixed rubber that improves chloroprene rubber scorch performance comprises the following steps:
[0034] (1) Initial mixing: Add 90 parts of neoprene to the internal mixer to press the top bolt, after 30 seconds, raise the top bolt and add 40 parts of carbon black, 15 parts of plasticizer and ...
PUM
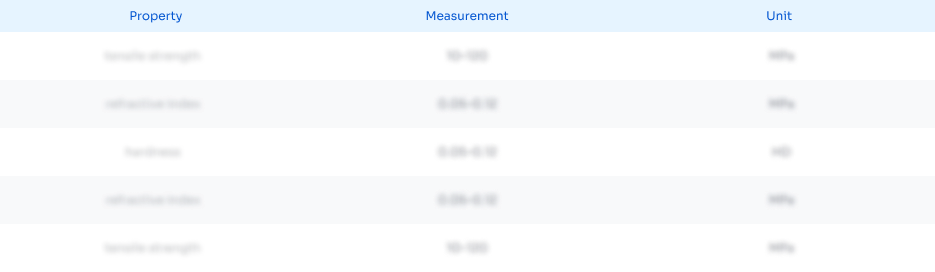
Abstract
Description
Claims
Application Information

- R&D
- Intellectual Property
- Life Sciences
- Materials
- Tech Scout
- Unparalleled Data Quality
- Higher Quality Content
- 60% Fewer Hallucinations
Browse by: Latest US Patents, China's latest patents, Technical Efficacy Thesaurus, Application Domain, Technology Topic, Popular Technical Reports.
© 2025 PatSnap. All rights reserved.Legal|Privacy policy|Modern Slavery Act Transparency Statement|Sitemap|About US| Contact US: help@patsnap.com