Method for oxidizing elemental mercury by improving gas selective catalytic reduction (SCR) denitration processing system
A treatment system and SCR catalyst technology, applied in chemical instruments and methods, separation methods, dispersed particle separation, etc., can solve the problem of low mercury oxidation efficiency and achieve the effect of improving the removal rate
- Summary
- Abstract
- Description
- Claims
- Application Information
AI Technical Summary
Problems solved by technology
Method used
Examples
Embodiment 1
[0012] A method for oxidizing elemental mercury by improving the flue gas SCR denitrification treatment system. The traditional SCR catalyst layer is arranged in front of the mercury oxidation catalyst, and then a layer of modified SCR catalyst is arranged as the mercury oxidation catalyst layer. In the traditional SCR catalytic system Inject NH 3 , NH 3 The molar ratio to NO is 0.6:1. The preparation method of the modified SCR catalyst is: adding transition metal oxides during the preparation of the SCR catalyst to modify it, that is, at V 2 o 5 -WO 3 / TiO 2 In the preparation of the SCR catalyst, after adding V 2 o 5 and WO 3 At the same time as the precursor, cerium nitrate was also added, and the mass of cerium nitrate added was 8% of the total amount of the catalyst based on Ce, and the removal efficiency of NO in flue gas was 80% at a temperature of 300-400 °C, and the oxidation efficiency of mercury 85%.
Embodiment 2
[0014] A method for oxidizing elemental mercury by improving the flue gas SCR denitrification treatment system. Before the traditional 4-layer SCR catalyst layer is arranged on the mercury oxidation catalyst, inject NH into the traditional SCR catalytic system 3 , NH 3 The molar ratio to NO is 1:1, and then two layers of modified SCR catalysts are arranged as the mercury oxidation catalytic layer. The preparation method of the modified SCR catalyst is: adding transition metal oxides during the preparation of the SCR catalyst to modify it. ie at V 2 o 5 -WO 3 / TiO 2 In the preparation of the SCR catalyst, after adding V 2 o 5 and WO 3 At the same time as the precursor, cerium nitrate was also added, and the mass of cerium nitrate added was 2% of the total amount of the catalyst based on Ce. The removal efficiency of NO in the flue gas was 95% at a temperature of 300-400 °C, and the oxidation efficiency of mercury was 95%. was 73%.
Embodiment 3
[0016] A method for oxidizing elemental mercury by improving the flue gas SCR denitrification treatment system. Before the traditional 3-layer SCR catalyst layer is arranged on the mercury oxidation catalyst, inject NH into the traditional SCR catalytic system 3 , NH 3 The molar ratio to NO is 0.9:1, and then a layer of modified SCR catalyst is arranged. The preparation method of the modified SCR catalyst is: adding transition metal oxides during the preparation of the SCR catalyst to modify it, that is, at V 2 o 5 -WO 3 / TiO 2 In the preparation of the SCR catalyst, after adding V 2 o 5 and WO 3 At the same time as the precursor, cerium nitrate was also added. The added mass of cerium nitrate was calculated as 4% of the total amount of catalyst based on Ce. The removal efficiency of NO in the flue gas was 85% at a temperature of 300-400 ° C. The oxidation of mercury The efficiency is 81%.
PUM
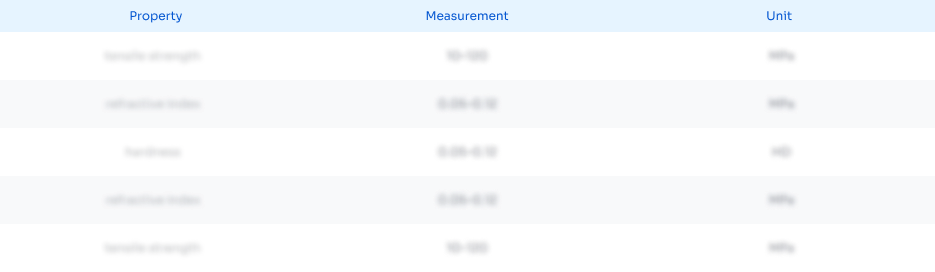
Abstract
Description
Claims
Application Information

- R&D
- Intellectual Property
- Life Sciences
- Materials
- Tech Scout
- Unparalleled Data Quality
- Higher Quality Content
- 60% Fewer Hallucinations
Browse by: Latest US Patents, China's latest patents, Technical Efficacy Thesaurus, Application Domain, Technology Topic, Popular Technical Reports.
© 2025 PatSnap. All rights reserved.Legal|Privacy policy|Modern Slavery Act Transparency Statement|Sitemap|About US| Contact US: help@patsnap.com