Method for prolonging service life of roller
A roll life, roll technology, applied in the direction of roll, metal rolling, metal rolling, etc., can solve the problems of roll wear consumption, affecting operation rate, spare parts consumption, etc., so as to save roll consumption cost, improve rolling mill operation rate, improve The effect of service life
- Summary
- Abstract
- Description
- Claims
- Application Information
AI Technical Summary
Problems solved by technology
Method used
Image
Examples
Embodiment Construction
[0014] The above-mentioned and other technical features and advantages of the present invention will be described in more detail below in conjunction with the embodiments.
[0015] Implementation steps:
[0016] (1) Turn the roll according to the drawing requirements;
[0017] (2) Carry out surface alloy spraying alloy powder with the roll that turning is good, described alloy powder comprises Cr, Si, Mo, W, mullite and rutile, and mass percent is: Cr8%, Si19%, Mo6%, W6% and molybdenum Come stone 30%, rutile 31%;
[0018] (3) Carry out laser point heating to melt the alloy and the roll matrix metal, so that the alloy forms point-shaped, discretely distributed alloying points, and the laser radiation power density is 104~105W / cm 2 ;
[0019] (4) Rapidly cooling and heat-treating the alloying point at a rate of 103-105°C / s, and the treated rolls are used on-line.
PUM
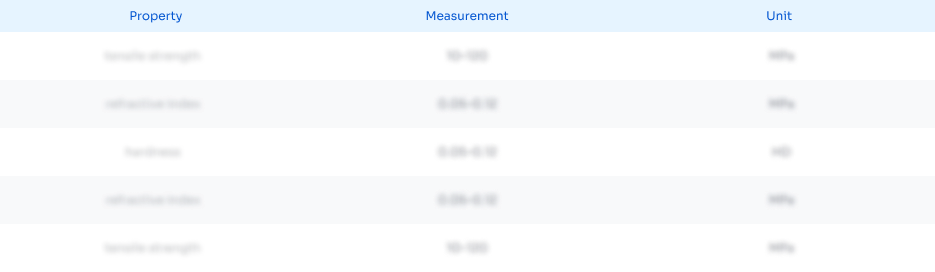
Abstract
Description
Claims
Application Information

- R&D Engineer
- R&D Manager
- IP Professional
- Industry Leading Data Capabilities
- Powerful AI technology
- Patent DNA Extraction
Browse by: Latest US Patents, China's latest patents, Technical Efficacy Thesaurus, Application Domain, Technology Topic, Popular Technical Reports.
© 2024 PatSnap. All rights reserved.Legal|Privacy policy|Modern Slavery Act Transparency Statement|Sitemap|About US| Contact US: help@patsnap.com