A negative thermal expansion material sc 2 w 3 o 12 Film Preparation Method
A negative thermal expansion material, sc2w3o12 technology, applied in metal material coating process, ion implantation plating, coating and other directions, can solve the problem of phase change negative thermal expansion response temperature range, difficult to achieve mass production, high heat treatment temperature, Achieve the effect of wide response temperature range of negative thermal expansion, easy batch and industrial production, and low heat treatment temperature
- Summary
- Abstract
- Description
- Claims
- Application Information
AI Technical Summary
Problems solved by technology
Method used
Image
Examples
Embodiment 1
[0024] 1. Target preparation:
[0025] Use scandium oxide and molybdenum oxide powder as raw materials, weigh them separately according to the molar ratio of 1:3 and mix them, add alcohol and then ball mill them for 12 hours. Grind in an agate mortar for 30 minutes, add polyvinyl alcohol (PVA) accounting for 3% of the total mass of the precursor, grind to make the mixture uniform, and then cold isostatic pressing at 50MPa, debinding at 500°C for 0.5h, and sintering at 950°C 24h, get Sc after cooling with the furnace 2 W 3 o 12 ceramic target;
[0026] 2. Clean and activate the monocrystalline silicon substrate using conventional processes;
[0027] Inject hydrogen peroxide into the beaker, and then inject concentrated H 2 SO 4, the ratio is 1:2, put the monocrystalline silicon substrate into it, clean it with ultrasonic for about 10min, pour out the washing liquid, and wash the beaker and the substrate with deionized water. Inject HF and deionized water into a plastic b...
Embodiment 2
[0033] 1. Target preparation:
[0034] Use scandium oxide and molybdenum oxide powders as raw materials, weigh them separately according to the molar ratio of 1:3 and mix them, add alcohol and then ball mill them for 18 hours, dry them in a vacuum drying oven at 80°C after ball milling, and use Grinding in an agate mortar for 20 min, adding polyvinyl alcohol (PVA) accounting for 4% of the total mass of the precursor, grinding to make the mixture uniform, and then cold isostatic pressing at 75MPa, debinding at 500°C for 0.7h, and then heating at 1100°C Sintered for 18 hours, and obtained Sc after cooling with the furnace 2 W 3 o 12 ceramic target;
[0035] 2. Clean and activate the monocrystalline silicon substrate using conventional processes;
[0036] Inject hydrogen peroxide into the beaker, and then inject concentrated H 2 SO 4 , the ratio is 1:2, put the monocrystalline silicon substrate into it, clean it with ultrasonic for about 10min, pour out the washing liquid, ...
Embodiment 3
[0042] 1. Target preparation:
[0043] Use scandium oxide and molybdenum oxide powder as raw materials, weigh them separately according to the molar ratio of 1:3 and mix them, add alcohol and then ball mill them for 24 hours. Grinding in an agate mortar for 10 min, adding polyvinyl alcohol (PVA) accounting for 5% of the total mass of the precursor, grinding to make the mixture uniform, and then cold isostatic pressing at 100MPa, debinding at 500°C for 1h, and sintering at 1200°C 12h, get Sc after cooling with the furnace 2 W 3 o 12 ceramic target;
[0044] 2. Clean and activate the monocrystalline silicon substrate using conventional processes;
[0045] Inject hydrogen peroxide into the beaker, and then inject concentrated H 2 SO 4 , the ratio is 1:2, put the monocrystalline silicon substrate into it, clean it with ultrasonic for about 10min, pour out the washing liquid, and wash the beaker and the substrate with deionized water. Inject HF and deionized water into a pla...
PUM
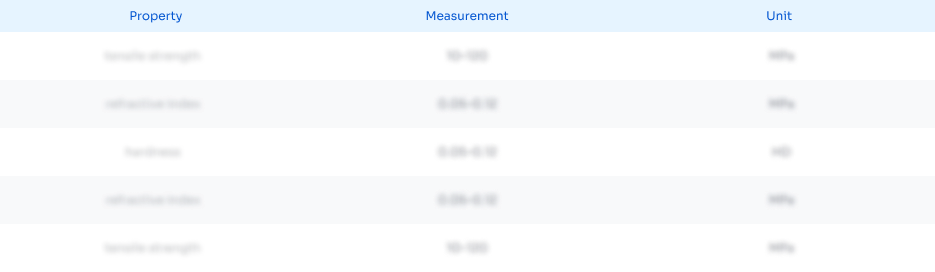
Abstract
Description
Claims
Application Information

- R&D Engineer
- R&D Manager
- IP Professional
- Industry Leading Data Capabilities
- Powerful AI technology
- Patent DNA Extraction
Browse by: Latest US Patents, China's latest patents, Technical Efficacy Thesaurus, Application Domain, Technology Topic, Popular Technical Reports.
© 2024 PatSnap. All rights reserved.Legal|Privacy policy|Modern Slavery Act Transparency Statement|Sitemap|About US| Contact US: help@patsnap.com