A boiler for galvanizing metal
A galvanizing and boiler technology, applied in metal material coating process, hot-dip plating process, coating, etc., can solve the problems of unfavorable long-term development of enterprises, low heating efficiency, short service life, etc., and achieve good insulation effect and use The effect of prolonging life and avoiding safety hazards
- Summary
- Abstract
- Description
- Claims
- Application Information
AI Technical Summary
Problems solved by technology
Method used
Image
Examples
Embodiment Construction
[0016] The present invention will be further described below in conjunction with accompanying drawing, protection scope of the present invention is not limited to the following:
[0017] Such as figure 1 As shown, a boiler for galvanizing metals includes a boiler body. The boiler body 1 is provided with a heating assembly 2 , and a zinc fume absorption device 3 is also provided on the side wall of the boiler body 1 .
[0018] In this example, if figure 1 and figure 2 As shown, the boiler body 1 is a square groove 11 set on the ground, its upper end is open, and the side wall of the square groove 11 is sequentially provided with a heat conducting layer 12, a pouring layer 10, a supporting layer 13, a partition The heat layer 14 and the concrete layer 15 are provided with an inner wall protection plate 16 on the inner side wall of the heat conduction layer 12, and a wall protection steel plate 17 is buried above the concrete layer 15, and a capping plate 18 is arranged betwee...
PUM
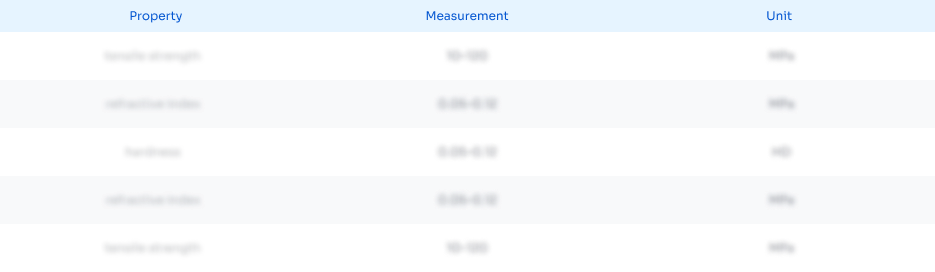
Abstract
Description
Claims
Application Information

- Generate Ideas
- Intellectual Property
- Life Sciences
- Materials
- Tech Scout
- Unparalleled Data Quality
- Higher Quality Content
- 60% Fewer Hallucinations
Browse by: Latest US Patents, China's latest patents, Technical Efficacy Thesaurus, Application Domain, Technology Topic, Popular Technical Reports.
© 2025 PatSnap. All rights reserved.Legal|Privacy policy|Modern Slavery Act Transparency Statement|Sitemap|About US| Contact US: help@patsnap.com