Cloth cutter for shoe making
A cloth cutting machine and cloth cutting technology, which is applied in the machinery, application, footwear and other directions of shoemaking, can solve the problems of die damage, cloth waste, and lengthening the production cycle of the shoemaking process, so as to save cloth and improve production. Efficiency, the effect of shortening the production cycle
- Summary
- Abstract
- Description
- Claims
- Application Information
AI Technical Summary
Problems solved by technology
Method used
Image
Examples
Embodiment Construction
[0024] Implementation column 1
[0025] Such as figure 1 As shown in figure 1 As shown in the figure, the cloth loading device (5) is arranged on the rear and upper side of the frame (1), the cloth stacking and cutting conveying device (4) is arranged on the frame (1), and the cloth cutting supports the conveying platform (3) It is arranged at the front of the frame (1), and the cloth cutting device (2) is arranged above the cloth cutting support and conveying platform (3);
[0026] Such as figure 2 As shown in the figure, the cloth adjusting rod (5-5) is set under the frame (1), the cloth rack (5-2) is connected with the lower end of the cloth adjusting rod (5-5), and the cloth rack (5-2) The middle part is set on the frame (1); the cloth stacking device fixing device (5-3) is set on the frame (1); the upper cloth fixing device (5-3) is provided with an upper cloth clamping device ( 5-6), the cloth pressing device (5-7) is arranged at the top of the cloth fixing device (5-3), a...
PUM
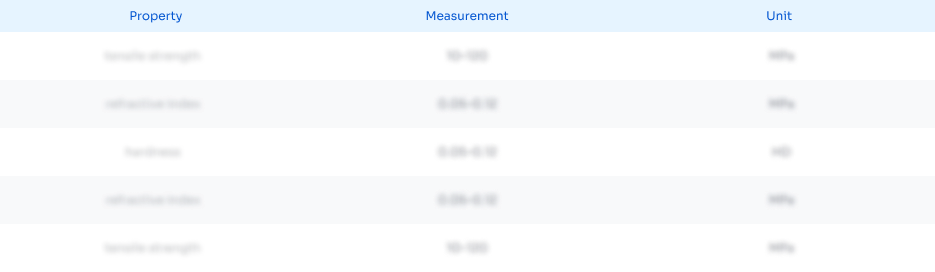
Abstract
Description
Claims
Application Information

- Generate Ideas
- Intellectual Property
- Life Sciences
- Materials
- Tech Scout
- Unparalleled Data Quality
- Higher Quality Content
- 60% Fewer Hallucinations
Browse by: Latest US Patents, China's latest patents, Technical Efficacy Thesaurus, Application Domain, Technology Topic, Popular Technical Reports.
© 2025 PatSnap. All rights reserved.Legal|Privacy policy|Modern Slavery Act Transparency Statement|Sitemap|About US| Contact US: help@patsnap.com