Five-phase permanent magnet fault-tolerant motor direct torque control method based on novel pulse width modulation
A technology of direct torque control and pulse width modulation, which is applied in motor generator control, AC motor control, electronic commutation motor control, etc. Torque and flux linkage pulsation problems, to achieve the effect of suppressing the third harmonic content, reducing the third harmonic content, reducing torque and flux linkage pulsation
- Summary
- Abstract
- Description
- Claims
- Application Information
AI Technical Summary
Problems solved by technology
Method used
Image
Examples
Embodiment Construction
[0046] The technical solutions in the embodiments of the present invention will be clearly and completely described below with reference to the accompanying drawings in the embodiments of the present invention.
[0047] The following describes in detail the embodiments of the present invention, examples of which are illustrated in the accompanying drawings, wherein the same or similar reference numerals refer to the same or similar elements or elements having the same or similar functions throughout. The embodiments described below with reference to the accompanying drawings are exemplary, only used to explain the present invention, and should not be construed as a limitation of the present invention.
[0048] The present invention is a direct torque control method for a five-phase permanent magnet fault-tolerant motor based on the ZVI-CPWM strategy. The specific principle block diagram is as follows: figure 1 shown. Given speed ω m * with the actual speed ω m The differen...
PUM
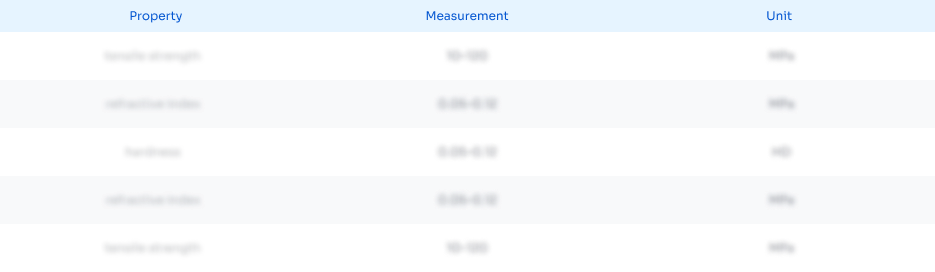
Abstract
Description
Claims
Application Information

- R&D
- Intellectual Property
- Life Sciences
- Materials
- Tech Scout
- Unparalleled Data Quality
- Higher Quality Content
- 60% Fewer Hallucinations
Browse by: Latest US Patents, China's latest patents, Technical Efficacy Thesaurus, Application Domain, Technology Topic, Popular Technical Reports.
© 2025 PatSnap. All rights reserved.Legal|Privacy policy|Modern Slavery Act Transparency Statement|Sitemap|About US| Contact US: help@patsnap.com