Overload-resistant capacitive triaxial MEMS accelerometer
An accelerometer, capacitive technology, applied in the measurement of acceleration, multi-dimensional acceleration measurement, speed/acceleration/shock measurement, etc., can solve the problems of increasing manufacturing cost, accelerometer not working, measurement inaccurate, etc., to avoid high overload shock , the mode shape is stable, and the effect of increasing the natural frequency
- Summary
- Abstract
- Description
- Claims
- Application Information
AI Technical Summary
Problems solved by technology
Method used
Image
Examples
Embodiment Construction
[0023] to combine Figure 1~3 As shown, the present invention provides an anti-overload capacitive three-axis MEMS accelerometer, including an X-axis detection unit 2, a Y-axis detection unit 3, and a Z-axis detection unit 1 disposed on a substrate;
[0024] The Z-axis detection unit 1 includes an H-shaped Z-axis mass block 1a, and the middle part of the Z-axis mass block 1a is provided with a Z-axis anchor body 1b and a Z-axis elastic beam 1c, and the Z-axis mass block 1a The two opening sides of the Z axis are respectively provided with mutually symmetrical Z-axis stress release beams, and each Z-axis stress release beam includes a first-level stress release beam 1f and a second-level stress release beam 1g in the shape of "冂", and a second-level stress release beam 1g. The stress release beam 1g spans the two ends corresponding to the opening side, and the primary stress release beam 1f is arranged in the middle outside the secondary stress release beam 1g; the length of th...
PUM
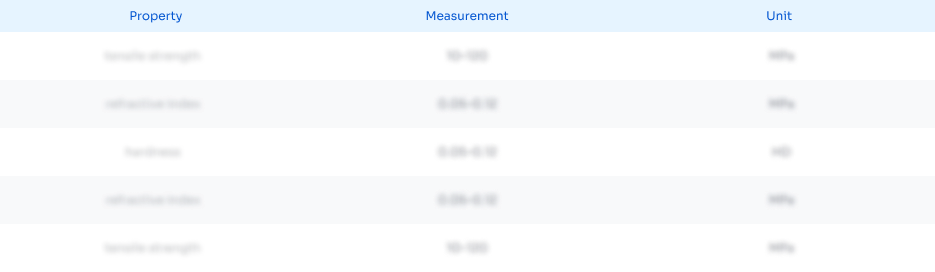
Abstract
Description
Claims
Application Information

- R&D Engineer
- R&D Manager
- IP Professional
- Industry Leading Data Capabilities
- Powerful AI technology
- Patent DNA Extraction
Browse by: Latest US Patents, China's latest patents, Technical Efficacy Thesaurus, Application Domain, Technology Topic, Popular Technical Reports.
© 2024 PatSnap. All rights reserved.Legal|Privacy policy|Modern Slavery Act Transparency Statement|Sitemap|About US| Contact US: help@patsnap.com