Centrifugal pendulum
A technology of centrifugal force pendulum and pendulum quality, applied in the field of centrifugal force pendulum, which can solve problems such as elastic body fracture, hydraulic or mechanical damage, and achieve the effect of improving manufacturability and reducing damage rate
- Summary
- Abstract
- Description
- Claims
- Application Information
AI Technical Summary
Problems solved by technology
Method used
Image
Examples
Embodiment Construction
[0022] figure 1 A first view is shown of a centrifugal force pendulum 100 for damping rotational or torsional vibrations, in particular in a drive train of a motor vehicle. The centrifugal pendulum 100 includes a pendulum flange 105 with an axis of rotation 110 and one or more pendulum masses 115 . In the illustrated embodiment, each pendulum mass 115 is formed by a first and a second mass element 120 , which are located on different axial sides of the pendulum flange 105 . In this illustration, pendulum masses 115 are each in a neutral position. Of the three pendulum masses 115 shown by way of example, only the mass element 120 remote from the observer is shown in each of the lower two pendulum masses. In the third pendulum mass 115 shown above, the mass element 120 facing the viewer is shown transparently.
[0023] Each pendulum mass 115 is mounted on the pendulum flange 105 displaceably in the plane of rotation of the pendulum flange 105 by means of one or more link guid...
PUM
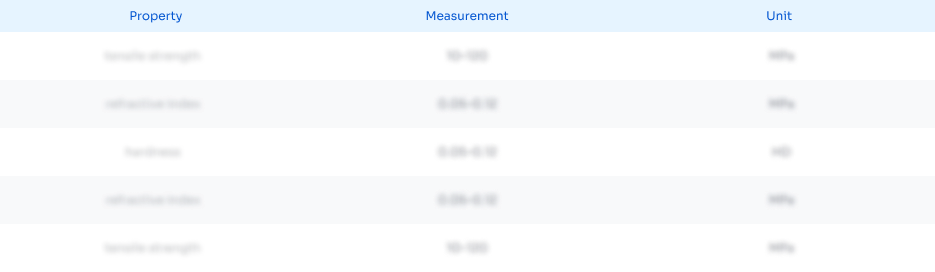
Abstract
Description
Claims
Application Information

- R&D
- Intellectual Property
- Life Sciences
- Materials
- Tech Scout
- Unparalleled Data Quality
- Higher Quality Content
- 60% Fewer Hallucinations
Browse by: Latest US Patents, China's latest patents, Technical Efficacy Thesaurus, Application Domain, Technology Topic, Popular Technical Reports.
© 2025 PatSnap. All rights reserved.Legal|Privacy policy|Modern Slavery Act Transparency Statement|Sitemap|About US| Contact US: help@patsnap.com