Spiral steering clamp for numerical control machine tool
A CNC machine tool and screw technology, applied in the direction of clamping, clamping device, manufacturing tool, etc., can solve the problems of vibration, easy deformation, inaccurate positioning, etc.
- Summary
- Abstract
- Description
- Claims
- Application Information
AI Technical Summary
Problems solved by technology
Method used
Image
Examples
Embodiment
[0024] When the product is processed, the product is first positioned, and the product is placed in the positioning block 5 along the product guide pin 4 for positioning, orientated by the orientation pin 6, and the product position is adjusted until the support nail 7 stabilizes the lower end surface of the product. The brake system pulls the pull rod 1 to drive the pull plate 9 to compress the spring 10, and transmits the elastic force to the steering shaft 12 through the thrust ball bearing 11 to make it pull down, the guide screw 13 moves along the spiral guide rail 16, and the pressure plate 3 turns and turns The product is pressed tightly. After the product is processed, the hydraulic mechanical brake system of the machine tool pushes out the tie rod 1, drives the pull plate 9, and pushes up the steering shaft 12 through the thrust ball bearing 11, so that the pressure plate 3 is released, and the product is taken out. The invention has the characteristics of no displacem...
PUM
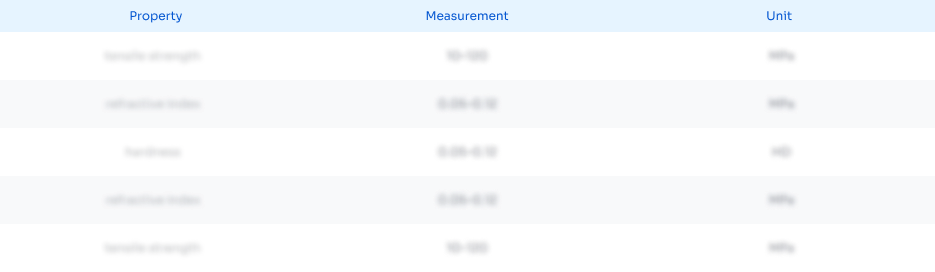
Abstract
Description
Claims
Application Information

- R&D
- Intellectual Property
- Life Sciences
- Materials
- Tech Scout
- Unparalleled Data Quality
- Higher Quality Content
- 60% Fewer Hallucinations
Browse by: Latest US Patents, China's latest patents, Technical Efficacy Thesaurus, Application Domain, Technology Topic, Popular Technical Reports.
© 2025 PatSnap. All rights reserved.Legal|Privacy policy|Modern Slavery Act Transparency Statement|Sitemap|About US| Contact US: help@patsnap.com