Microstructure laser-induce implantation method and device based on turbid liquid target
A microstructure, laser-induced technology, applied in laser welding equipment, welding equipment, metal processing equipment, etc., can solve problems such as difficulty, easy consumption, and difficulty in guaranteeing, and achieve the effect of improving surface performance, increasing manufacturing efficiency, and improving efficiency.
- Summary
- Abstract
- Description
- Claims
- Application Information
AI Technical Summary
Problems solved by technology
Method used
Image
Examples
Embodiment Construction
[0026] The following will clearly and completely describe the technical solutions in the embodiments of the present invention with reference to the accompanying drawings in the embodiments of the present invention. Obviously, the described embodiments are only some, not all, embodiments of the present invention. Based on the embodiments of the present invention, all other embodiments obtained by persons of ordinary skill in the art without creative efforts fall within the protection scope of the present invention.
[0027] see image 3 , a structural schematic diagram of a method for laser-induced implantation of microstructures based on a suspension target and a device for implementing the method provided by a preferred embodiment of the present invention.
[0028]In the laser-induced implantation method of microstructure based on the suspension liquid target in this embodiment, the laser 1 generates a high-energy pulsed laser 5 , and the energy and frequency of the laser are...
PUM
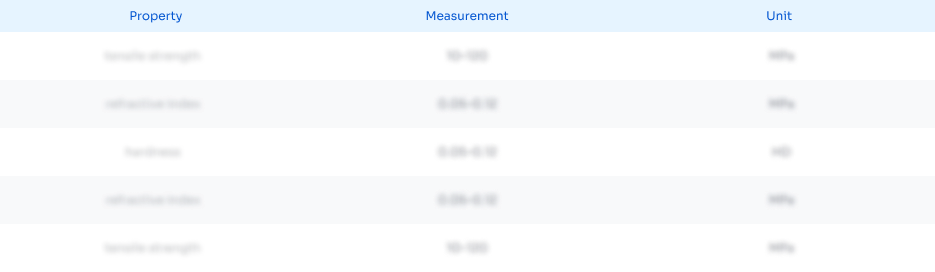
Abstract
Description
Claims
Application Information

- Generate Ideas
- Intellectual Property
- Life Sciences
- Materials
- Tech Scout
- Unparalleled Data Quality
- Higher Quality Content
- 60% Fewer Hallucinations
Browse by: Latest US Patents, China's latest patents, Technical Efficacy Thesaurus, Application Domain, Technology Topic, Popular Technical Reports.
© 2025 PatSnap. All rights reserved.Legal|Privacy policy|Modern Slavery Act Transparency Statement|Sitemap|About US| Contact US: help@patsnap.com