Efficient micro-machining method and device for non-conductive crisp and hard material
A technology of hard and brittle materials and processing methods, applied in stone processing equipment, stone processing tools, manufacturing tools, etc., can solve the problems of easy generation of micro-cracks and thermal stress, difficult to achieve micro-processing of parts, and macro-cutting forces. Achieve the effect of improving machining accuracy and surface quality, optimizing the gap electric field, and reducing production costs
- Summary
- Abstract
- Description
- Claims
- Application Information
AI Technical Summary
Problems solved by technology
Method used
Image
Examples
Embodiment 1
[0017] A micro-high-efficiency machining method for non-conductive hard and brittle materials—ultrasonic electrolysis-EDM micromachining, using micro-electrolysis-EDM to process workpieces with ultrasonic excitation; the power supply of the electrolysis-EDM unit adopts DC high-frequency pulse power supply ; The tool electrode is helical and rotates at high speed during machining.
[0018] Ultrasonic electrolysis-EDM micromachining device, including electrolysis-EDM unit, ultrasonic vibration table and feed table, etc. The electrolysis-EDM unit is composed of spindle 1, tool electrode 2, electrolyte 3, workpiece 4, feed table 8, auxiliary electrode 10 and electrolysis-EDM power supply 11; the tool electrode 2, auxiliary electrode 10 and workpiece 4 are submerged In the electrolyte 3; the tool electrode 2 is connected to the negative pole of the power supply, and the auxiliary electrode 10 is connected to the positive pole of the power supply; the main shaft 1 has a displacement...
Embodiment 2
[0021] The electrolysis-spark power supply 11 adopts a DC pulse power supply, the electrolyte solution 3 adopts a sodium hydroxide solution, and others are as in Example 1.
Embodiment 3
[0023] The tool electrode 2 is made of a steel needle, and the horn 6 and the vibrating disc 5, and the vibrating disc 5 and the workpiece 4 are fixedly connected by bonding, and others are as in Example 1.
[0024] The method of the present invention has the advantages of high precision of low-voltage discharge, and can also obtain good surface quality; the method of the present invention makes the workpiece perform ultrasonic vibration, making the processing process more stable, and the ultrasonic vibration of the workpiece and the high-speed rotation of the spiral electrode greatly improve the Processing efficiency; the method of the present invention is easy to realize fine, precise and high-efficiency processing in terms of processing mechanism, and the production cost is low; the method of the present invention is especially suitable for the micro-processing of non-conductive hard and brittle materials, which is conducive to improving processing accuracy and surface qualit...
PUM
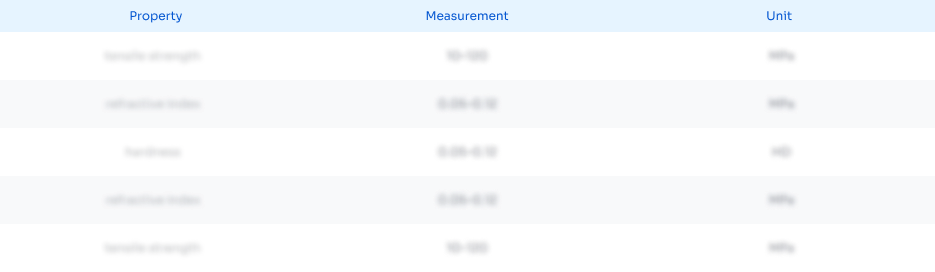
Abstract
Description
Claims
Application Information

- R&D
- Intellectual Property
- Life Sciences
- Materials
- Tech Scout
- Unparalleled Data Quality
- Higher Quality Content
- 60% Fewer Hallucinations
Browse by: Latest US Patents, China's latest patents, Technical Efficacy Thesaurus, Application Domain, Technology Topic, Popular Technical Reports.
© 2025 PatSnap. All rights reserved.Legal|Privacy policy|Modern Slavery Act Transparency Statement|Sitemap|About US| Contact US: help@patsnap.com