Catalyst replacement system and method for slurry bed reactor
A replacement method and reactor technology, applied in chemical instruments and methods, chemical/physical processes, preparation of liquid hydrocarbon mixtures, etc., can solve the problems of reduced reaction efficiency, reduced product price, pipeline blockage, etc., and reduced production and maintenance costs. , the effect of stabilizing product quality and increasing product output
- Summary
- Abstract
- Description
- Claims
- Application Information
AI Technical Summary
Problems solved by technology
Method used
Image
Examples
Embodiment 1
[0022] Such as figure 1 Shown, the slurry bed reactor catalyst replacement system comprises a slurry bed reactor 1, a reduction reactor 2 and a slag wax stirred tank 3, and the feed port of the reduction reactor 2 is connected with one end of the feed line 4, and the The feed line 4 is sequentially provided with a first feed valve 5, a second feed valve 6 and a third feed valve 7 starting from the feed port of the reduction reactor 2; The pipeline 8 is connected to the feed port of the slurry bed reactor 1, and the discharge line 8 is provided with the first discharge port in turn from the discharge port end of the reduction reactor 2 to the feed port end of the slurry bed reactor 2. The valve 9 and the second discharge valve 10; the first pipeline 11 is arranged between the feed pipeline 4 and the discharge pipeline 8, and the feed port of the first pipeline 11 is connected with the first discharge valve 9 and the second discharge valve 9 The discharge pipeline 8 between the...
Embodiment 2
[0024] A method of combining regular catalyst replacement with a large number of catalyst replacements is adopted. The specific catalyst replacement is that the catalyst is replaced every 5 days, and the amount of catalyst is 4.5 tons each time. The catalyst is replaced in a large number, and the catalyst will be restored twice in a row once a month. The catalyst is added to the slurry bed reactor at one time to complete a large number of replacements, such as figure 1 As shown, it specifically includes the following steps: a, storing the first part of the catalyst after pretreatment; b, using the second part of the catalyst after pretreatment; c, pressing the first part of the stored catalyst into the reduction reactor 2; d, in the reduction reactor 2 The first part of the catalyst is pressed into the slurry bed reactor 1 to complete a large amount of replacement of the catalyst; wherein,
[0025] a. The first part of the catalyst is stored after pretreatment: the catalyst is...
Embodiment 3
[0032] A method of combining regular catalyst replacement with a large number of catalyst replacements is adopted. The specific catalyst replacement is that the catalyst is replaced every 5 days, and the amount of catalyst is 4.5 tons each time. The catalyst is replaced in a large number, and the catalyst will be restored twice in a row once a month. The catalyst is added to the slurry bed reactor at one time to complete a large number of replacements, such as figure 1 As shown, it specifically includes the following steps: a, storing the first part of the catalyst after pretreatment; b, using the second part of the catalyst after pretreatment; c, pressing the first part of the stored catalyst into the reduction reactor 2; d, in the reduction reactor 2 The first part of the catalyst is pressed into the slurry bed reactor 1 to complete a large amount of replacement of the catalyst; wherein,
[0033] a. The first part of the catalyst is stored after pretreatment: the catalyst is...
PUM
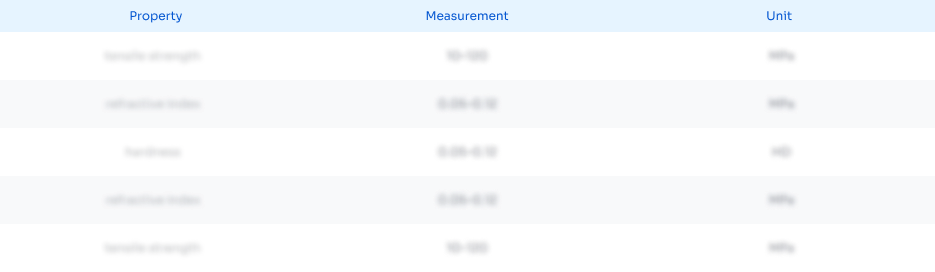
Abstract
Description
Claims
Application Information

- R&D Engineer
- R&D Manager
- IP Professional
- Industry Leading Data Capabilities
- Powerful AI technology
- Patent DNA Extraction
Browse by: Latest US Patents, China's latest patents, Technical Efficacy Thesaurus, Application Domain, Technology Topic, Popular Technical Reports.
© 2024 PatSnap. All rights reserved.Legal|Privacy policy|Modern Slavery Act Transparency Statement|Sitemap|About US| Contact US: help@patsnap.com