Phenolic foam heat insulation board of core-shell structure and preparing method thereof
A technology of foam insulation board and core-shell structure, applied in the field of phenolic foam insulation board and its preparation, can solve the problems of low toughness and easy breakage of phenolic foam, improve water absorption and comprehensive performance, reduce the possibility of fracture, and improve thermal conductivity. The effect of coefficient reduction
- Summary
- Abstract
- Description
- Claims
- Application Information
AI Technical Summary
Problems solved by technology
Method used
Image
Examples
Embodiment 1
[0036] (1) Add phenol, paraformaldehyde, and sodium hydroxide to the reaction kettle at a mass ratio of 65:30:1, add solid paraformaldehyde in batches at a water bath temperature of 60°C, control the addition for half an hour, and continue the reaction for half an hour hours, raise the temperature to 90°C, and continue the reaction for 1.5 hours to obtain the phenolic resin. Take 100.0 parts of phenolic resin, 6.0 parts of surfactant, 15 parts of foaming agent n-pentane, 15 parts of curing agent, and 1 part of nucleating agent, mix and stir evenly for use.
[0037] (2) Take 100 parts of polyethylene adipate diol (PEA2000), 10 parts of toluene diisocyanate (TDI-80), and 0.1 part of dibutyltin dilaurate (DBTDL) into the reaction kettle, 80 ℃ Under vacuum reaction for 1h, the polyurethane prepolymer was obtained. Take 100 parts of polyurethane prepolymer, 2 parts of foam stabilizer, and 12 parts of foaming agent, mix and stir evenly for use.
[0038] (3) Reaction kettles A and ...
Embodiment 2
[0040](1) Add phenol, paraformaldehyde, and sodium hydroxide to the reaction kettle at a mass ratio of 65:35:1, add solid paraformaldehyde in batches at a water bath temperature of 60°C, control the addition for half an hour, and continue the reaction for half an hour hours, raise the temperature to 90°C, and continue to react
[0041] It should take 1.5 hours to obtain phenolic resin. Take 100.0 parts of phenolic resin, 6.0 parts of surfactant, 15 parts of foaming agent n-pentane, 15 parts of curing agent, and 1 part of nucleating agent, mix and stir evenly for use.
[0042] (2) Take 100 parts of polyethylene adipate diol (PEA2000), 10 parts of toluene diisocyanate (TDI-80), and 0.1 part of dibutyltin dilaurate (DBTDL) into the reaction kettle, 80 ℃ Under vacuum reaction for 1h, the polyurethane prepolymer was obtained. Take 100 parts of polyurethane prepolymer, 2 parts of foam stabilizer, and 12 parts of foaming agent, mix and stir evenly for use.
[0043] (3) Same as ste...
Embodiment 3
[0045] (1) Add phenol, paraformaldehyde, and sodium hydroxide to the reaction kettle at a mass ratio of 65:40:1, add solid paraformaldehyde in batches at a water bath temperature of 60°C, control the addition for half an hour, and continue the reaction for half an hour hours, raise the temperature to 90°C, and continue the reaction for 1.5 hours to obtain the phenolic resin. Take 100.0 parts of phenolic resin, 6.0 parts of surfactant, 15 parts of foaming agent n-pentane, 15 parts of curing agent, and 1 part of nucleating agent, mix and stir evenly for use.
[0046] (2) Take 100 parts of polyethylene adipate diol (PEA2000), 10 parts of toluene diisocyanate (TDI-80), and 0.1 part of dibutyltin dilaurate (DBTDL) into the reaction kettle, 80 ℃ Under vacuum reaction for 1h, the polyurethane prepolymer was obtained. Take 100 parts of polyurethane prepolymer, 2 parts of foam stabilizer, and 12 parts of foaming agent, mix and stir evenly for use.
[0047] (3) Same as step 3 of Examp...
PUM
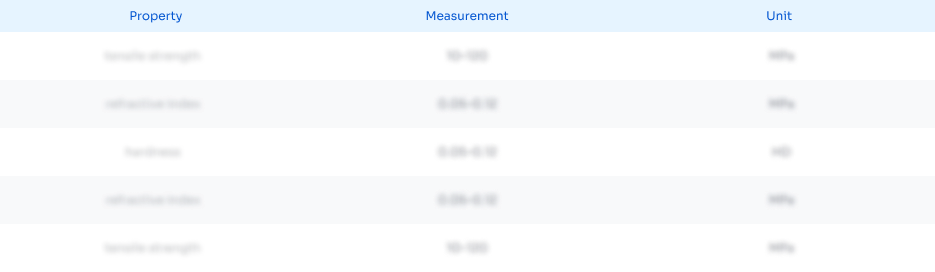
Abstract
Description
Claims
Application Information

- R&D Engineer
- R&D Manager
- IP Professional
- Industry Leading Data Capabilities
- Powerful AI technology
- Patent DNA Extraction
Browse by: Latest US Patents, China's latest patents, Technical Efficacy Thesaurus, Application Domain, Technology Topic.
© 2024 PatSnap. All rights reserved.Legal|Privacy policy|Modern Slavery Act Transparency Statement|Sitemap