Hydrotalcite composite flame retardant and preparation method thereof
A composite flame retardant and hydrotalcite technology, applied in the field of flame retardants, can solve the problems of poor thermal stability and affect the flame retardant performance of nano-composite materials, and achieve good flame retardant effect, reduce secondary harm, and reduce costs. Effect
- Summary
- Abstract
- Description
- Claims
- Application Information
AI Technical Summary
Problems solved by technology
Method used
Image
Examples
Embodiment 1
[0023] Mix 1.31g of 6-aminocaproic acid and 10mL of sodium hydroxide with a concentration of 1.0mol / L to form a 6-aminocaproic acid sodium solution, then add 0.8L of distilled water and 97g of hydrotalcite to a 1L stainless steel reactor, and heat to 80 ℃ and vigorously stirred for 2 hours, added the above sodium 6-aminocaproate solution, stirred vigorously at 90℃ for 12 hours, washed the product obtained by filtration with distilled water several times, dried the obtained solid in vacuum to constant weight, and obtained aminocaproic acid Acid-modified hydrotalcite.
[0024] Add 9.816g of aminocaproic acid modified hydrotalcite to 100mL of toluene, ultrasonically disperse for 30 minutes, transfer it to a dry four-necked flask equipped with a mechanical stirrer, a thermometer, a reflux condenser, and a dropping funnel, and add dropwise 0.184g of 2- Mixture of oxo-2-chloro-5,5-dimethyl-1,3,2-dioxaphosphorinane and 10mL toluene, stirred and reacted at 15°C for 6 hours, then filte...
Embodiment 2
[0026] Mix 0.414g of 6-aminocaproic acid and 3.2mL of sodium hydroxide with a concentration of 1.0mol / L to form a 6-aminocaproic acid sodium solution, then add 0.8L of distilled water and 91g of hydrotalcite to a 1L stainless steel reactor, and heat to Stir vigorously at 90°C for 2 hours, add the above sodium 6-aminocaproate solution, stir vigorously at 90°C for 12 hours, wash the product obtained by filtration with distilled water several times, and dry the obtained solid in vacuum to constant weight to obtain Aminocaproic acid modified hydrotalcite.
[0027] Add 9.448g of aminocaproic acid modified hydrotalcite to 100mL of toluene, ultrasonically disperse for 30 minutes, transfer it to a dry four-necked flask equipped with a mechanical stirrer, a thermometer, a reflux condenser and a dropping funnel, and drop 0.552g of 2- Mixture of oxo-2-chloro-5,5-dimethyl-1,3,2-dioxaphosphorinane and 10mL toluene, stirred and reacted at 5°C for 10 hours, then filtered the suspension obtai...
Embodiment 3
[0029] Mix 13.8g of 6-aminocaproic acid and 100.5mL of sodium hydroxide with a concentration of 1.0mol / L to form a 6-aminocaproic acid sodium solution, then add 0.8L of distilled water and 70g of hydrotalcite to a 1L stainless steel reaction kettle, and heat to Stir vigorously at 80°C for 2 hours, add the above sodium 6-aminocaproate solution, stir vigorously at 80°C for 12 hours, wash the product obtained by filtration with distilled water at 80°C for several times, and dry the obtained solid in vacuum at 70°C to constant weight to obtain aminocaproic acid modified hydrotalcite.
[0030] Add 7.96g of aminocaproic acid modified hydrotalcite into 100mL of toluene, ultrasonically disperse it for 30 minutes, transfer it to a dry four-necked flask equipped with a mechanical stirrer, a thermometer, a reflux condenser and a dropping funnel, and add dropwise 1.84g of 2- Mixture of oxo-2-chloro-5,5-dimethyl-1,3,2-dioxaphosphorinane and 45mL toluene, stirred and reacted at 30°C for 7 h...
PUM
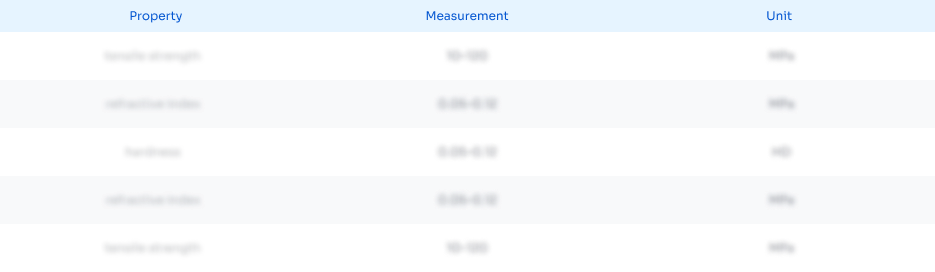
Abstract
Description
Claims
Application Information

- R&D
- Intellectual Property
- Life Sciences
- Materials
- Tech Scout
- Unparalleled Data Quality
- Higher Quality Content
- 60% Fewer Hallucinations
Browse by: Latest US Patents, China's latest patents, Technical Efficacy Thesaurus, Application Domain, Technology Topic, Popular Technical Reports.
© 2025 PatSnap. All rights reserved.Legal|Privacy policy|Modern Slavery Act Transparency Statement|Sitemap|About US| Contact US: help@patsnap.com