Ceramic alloy powder special for continuous optical fiber laser alloying
A ceramic alloy and fiber laser technology, which is applied in the field of ceramic alloy powder, can solve the problems of low level and achieve the effects of dense and uniform structure, reduced pores, and excellent anti-friction and wear properties
- Summary
- Abstract
- Description
- Claims
- Application Information
AI Technical Summary
Problems solved by technology
Method used
Examples
Embodiment 1
[0017] Embodiment 1: the proportioning of the weight percent of the ceramic alloy powder that is used for continuous fiber laser alloying is: 6% calcium fluoride, 9% boron, 3% lanthanum oxide, 20% silicon nitride, 3% tungsten carbide and 15 % titanium carbide.
Embodiment 2
[0018] Embodiment 2: will be 5% calcium fluoride by weight percentage, 8% boron, 3% lanthanum oxide, 15% silicon nitride; 3% tungsten carbide, the ratio of 10% titanium carbide weighs 500g sample, after sample preparation Obtain 200-300 mesh ceramic alloy powder.
Embodiment 3
[0019] Embodiment 3: will be 6% calcium fluoride by weight percentage, 9% boron, 4% lanthanum oxide, 20% silicon nitride; 5% tungsten carbide, the ratio of 13% titanium carbide weighs 500g sample, after sample preparation Obtain 200-300 mesh ceramic alloy powder.
PUM
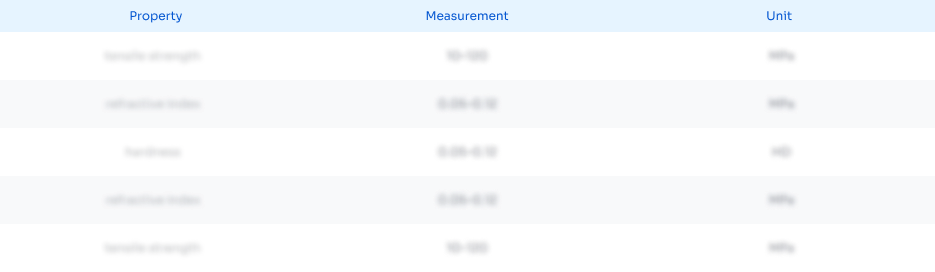
Abstract
Description
Claims
Application Information

- R&D
- Intellectual Property
- Life Sciences
- Materials
- Tech Scout
- Unparalleled Data Quality
- Higher Quality Content
- 60% Fewer Hallucinations
Browse by: Latest US Patents, China's latest patents, Technical Efficacy Thesaurus, Application Domain, Technology Topic, Popular Technical Reports.
© 2025 PatSnap. All rights reserved.Legal|Privacy policy|Modern Slavery Act Transparency Statement|Sitemap|About US| Contact US: help@patsnap.com