Lightweight design method for arm structure of assembly robot
A lightweight design, robot arm technology, applied in the field of robotics, can solve the problems of harsh load conditions, not considering the influence of the optimal design of the inertial load structure, and not giving the load acquisition method, so as to improve the movement speed and improve the assembly efficiency. , the effect of reducing weight
- Summary
- Abstract
- Description
- Claims
- Application Information
AI Technical Summary
Problems solved by technology
Method used
Image
Examples
Embodiment Construction
[0044] The present invention will be further elaborated below by describing a preferred specific embodiment in detail in conjunction with the accompanying drawings.
[0045] A lightweight design method for the arm structure of an assembled robot, which combines multi-body dynamics simulation with finite element simulation to obtain the load case with the largest stress in the arm's motion cycle, and performs topology optimization of the structure based on this load case Design, get the lightest design of the arm structure.
[0046] Such as figure 2 As shown, the robot includes a large arm 2, a small arm 3 and other parts, and the other parts include a base 1, a screw 4, and a main shaft 5, and the base 1 is fixed on the ground to drive the large arm. The motor and harmonic reducer for arm 2 rotation are fixed on the base 1, the motor and harmonic reducer for driving arm 3 to rotate are fixed on arm 3, and the lead screw is realized by the rotation of the motor installed on a...
PUM
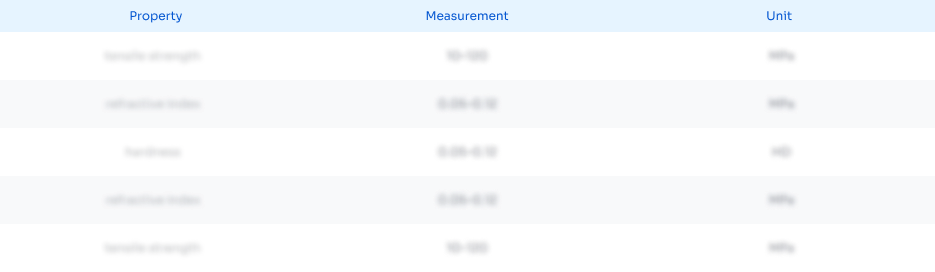
Abstract
Description
Claims
Application Information

- R&D
- Intellectual Property
- Life Sciences
- Materials
- Tech Scout
- Unparalleled Data Quality
- Higher Quality Content
- 60% Fewer Hallucinations
Browse by: Latest US Patents, China's latest patents, Technical Efficacy Thesaurus, Application Domain, Technology Topic, Popular Technical Reports.
© 2025 PatSnap. All rights reserved.Legal|Privacy policy|Modern Slavery Act Transparency Statement|Sitemap|About US| Contact US: help@patsnap.com