Material supply device for producing glass
A feeding device and glass technology, which is applied to the feeding of melting furnaces, glass manufacturing equipment, manufacturing tools, etc., can solve the problems of uneven feeding, deformation of feeding plates, affecting glass production work, etc., and achieve the effect of uniform feeding
- Summary
- Abstract
- Description
- Claims
- Application Information
AI Technical Summary
Problems solved by technology
Method used
Image
Examples
Embodiment Construction
[0023] like Figure 1 to Figure 6 Shown is a feeding device for glass production according to the present invention, which includes a glass cellar 1 , a feeder 2 and a control system 3 . The glass cellar 1 is mainly to melt the glass batch material into a liquid phase under a reasonable temperature system, and homogenize and clarify it to make it a transparent liquid. In the glass cellar 1, it is necessary to melt the glass liquid, glass Forming of products and annealing preparation of glass products. The selected glass cellar 1 can generally produce 50-150 tons per day, and the melting area is about 30-60 tons / ㎡. During the glass preparation process, the control system 3 controls the feeder 2 to supply materials to the glass cellar 1 .
[0024]The feeder 2 includes a frame 4 , a motor 5 and a transmission system 6 . A separate motor mounting seat is generally arranged in the frame 4, and the motor 5 is arranged on the motor mounting seat, and the motor mounting seat can sl...
PUM
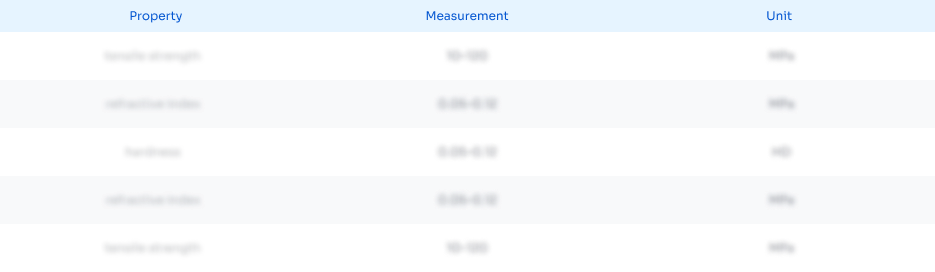
Abstract
Description
Claims
Application Information

- R&D Engineer
- R&D Manager
- IP Professional
- Industry Leading Data Capabilities
- Powerful AI technology
- Patent DNA Extraction
Browse by: Latest US Patents, China's latest patents, Technical Efficacy Thesaurus, Application Domain, Technology Topic, Popular Technical Reports.
© 2024 PatSnap. All rights reserved.Legal|Privacy policy|Modern Slavery Act Transparency Statement|Sitemap|About US| Contact US: help@patsnap.com