Electrothermal alloy material with excellent high temperature oxidation resistance and preparation method thereof
A high-temperature oxidation-resistant and electrothermal alloy technology, which is applied in the field of steel alloy materials, can solve the problems of difficult to meet operating temperature and high price, and achieve the effects of overcoming high-temperature embrittlement, improving oxidation resistance, and improving thermal strength
- Summary
- Abstract
- Description
- Claims
- Application Information
AI Technical Summary
Problems solved by technology
Method used
Image
Examples
Embodiment 1
[0015] In this embodiment, the composition and mass percentage of the electrothermal alloy material with excellent high-temperature oxidation resistance are as follows:
[0016] Cr 21.23%
[0017] Al 6.03%
[0018] Co 1.33%
[0019] Zr 0.14%
[0020] Rare earth Y 0.04%
[0021] Nb 0.43%
[0022] Mn 0.23%
[0023] Si 0.18%
[0024] C 0.016%
[0025] N 0.015%
[0026] S 0.008%
[0027] P 0.009%
[0028] Fe balance
[0029] Vacuum induction smelting is adopted, after comprehensive measurement calculation and batching smelting, casting and molding, and then hot forging, hot rolling, recrystallization heat treatment, cold rolling and cold drawing, and finally obtained Zr and rare earth Y alloy elements with excellent high temperature resistance An electrothermal alloy material with oxidation performance, its oxidation weight gain is about 6.98 mg / cm after isothermal oxidation at 1300°C for 360 hours 2 , and its oxidation weight gain curve follows a parabolic law.
Embodiment 2
[0031] In this embodiment, the electrothermal alloy material does not contain Zr and rare earth Y alloy elements, and the composition and weight percentage of the electrothermal alloy material are as follows:
[0032] Cr 21.34%
[0033] Al 5.98%
[0034] Co 1.41%
[0035] Nb 0.48%
[0036] Mn 0.21%
[0037] Si 0.19%
[0038] C 0.016%
[0039] N 0.017%
[0040] S 0.009%
[0041] P 0.007%
[0042] Fe balance
[0043] Vacuum induction smelting is adopted, after comprehensive measurement calculation and batching smelting, casting and forming, and then hot forging, hot rolling, recrystallization heat treatment, cold rolling and cold drawing, and finally the electrothermal alloy material without Zr and rare earth Y alloy elements is obtained. , its oxidation weight gain is about 12.17 mg / cm after isothermal oxidation at 1300°C for 360 hours 2 , and its oxidation weight gain curve also follows the parabolic law.
[0044] see figure 1 As shown, the oxidation weight gain of...
Embodiment 3
[0046] In this embodiment, the composition and mass percentage of the electrothermal alloy material with excellent high-temperature oxidation resistance are as follows:
[0047] Cr 22.65%
[0048] Al 5.68%
[0049] Co 0.6%
[0050] Zr 0.18%
[0051] Rare earth Y 0.04%
[0052] Nb 0.12%
[0053] Mn 0.33%
[0054] Si 0.18%
[0055] C 0.029%
[0056] N 0.015%
[0057] S 0.008%
[0058] P 0.009%
[0059] Fe balance
[0060] Vacuum induction smelting is adopted, after comprehensive measurement calculation and batching smelting, casting and molding, and then hot forging, hot rolling, recrystallization heat treatment, cold rolling and cold drawing, and finally obtained Zr and rare earth Y alloy elements with excellent high temperature resistance An electrothermal alloy material with oxidation performance, its oxidation weight gain is about 7.39 mg / cm after isothermal oxidation at 1300°C for 360 hours 2 , and its oxidation weight gain curve follows a parabolic law.
PUM
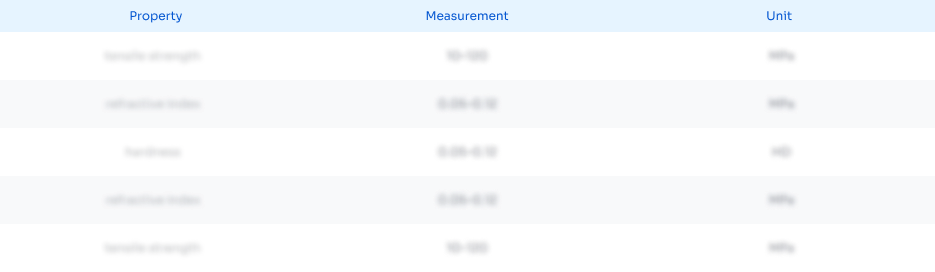
Abstract
Description
Claims
Application Information

- R&D Engineer
- R&D Manager
- IP Professional
- Industry Leading Data Capabilities
- Powerful AI technology
- Patent DNA Extraction
Browse by: Latest US Patents, China's latest patents, Technical Efficacy Thesaurus, Application Domain, Technology Topic, Popular Technical Reports.
© 2024 PatSnap. All rights reserved.Legal|Privacy policy|Modern Slavery Act Transparency Statement|Sitemap|About US| Contact US: help@patsnap.com