A self-deformable robot module unit and a snake-like robot
A snake-shaped robot and modular unit technology, applied in the field of robotics, can solve the problems of less motion forms, less robot configurations, and inability to biologically simulate motion, etc., and achieve the effects of strong motion ability, reasonable design and simple structure
- Summary
- Abstract
- Description
- Claims
- Application Information
AI Technical Summary
Problems solved by technology
Method used
Image
Examples
specific Embodiment approach 1
[0010] Embodiment 1: Combining Figure 1-Figure 3 Description, a self-deforming robot module unit in this embodiment includes a housing 1, a motor base 2, a motor 3, a first gear 6, a second gear 8, an output shaft 9, a cover 15, and a plurality of permanent magnets 10;
[0011] A motor base 2, a motor 3, a first gear 6, a second gear 8, an output shaft 9 and a plurality of permanent magnets 10 are arranged in the housing 1;
[0012] The motor base 2 is installed on the housing 1, the motor 3 is installed on the motor base 2, the output shaft 9 is rotatably installed on the motor base 2, the output shaft of the motor 3 is fixedly mounted with the first gear 6, and the second gear 8 is fixedly mounted on the motor base 2. On the output shaft 9, the first gear 6 meshes with the second gear 8, the cover plate 15 covers the surface opening of the casing 1, the cover plate 15 is made of martensitic stainless steel or ferritic stainless steel, and the end of the output shaft 9 The ...
specific Embodiment approach 2
[0014] Specific implementation mode 2: Combining figure 1 Note that the motor 3 of the present embodiment is a DC motor. This arrangement is cheap and easy to obtain, small in size and convenient to use, and a DC geared motor can be used. Others are the same as the first embodiment.
specific Embodiment approach 3
[0015] Specific implementation three: combination figure 1 It is explained that the plurality of permanent magnets 10 in this embodiment are glued on the disc structure 9 - 1 at the end of the output shaft 9 . With this setting, the connection is convenient and the use is reliable. Others are the same as in the first or second embodiment.
PUM
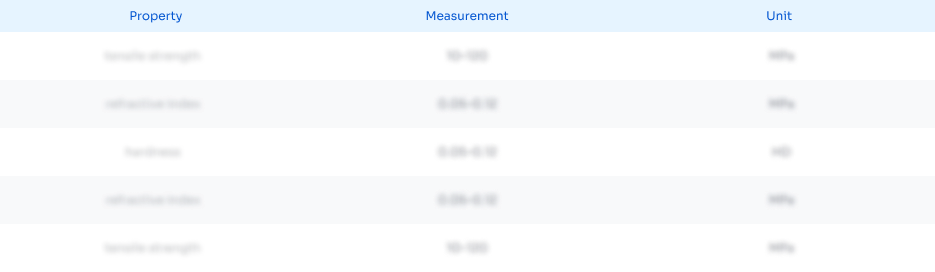
Abstract
Description
Claims
Application Information

- Generate Ideas
- Intellectual Property
- Life Sciences
- Materials
- Tech Scout
- Unparalleled Data Quality
- Higher Quality Content
- 60% Fewer Hallucinations
Browse by: Latest US Patents, China's latest patents, Technical Efficacy Thesaurus, Application Domain, Technology Topic, Popular Technical Reports.
© 2025 PatSnap. All rights reserved.Legal|Privacy policy|Modern Slavery Act Transparency Statement|Sitemap|About US| Contact US: help@patsnap.com