Automatic back-washing plate frame filter
A plate-and-frame filter, automatic backwashing technology, applied in filtration separation, separation methods, chemical instruments and methods, etc., can solve the problems of high operating cost, high consumption of filter cloth, difficult repair, etc., and achieve high filtration quality, High filtration efficiency and manpower saving effect
- Summary
- Abstract
- Description
- Claims
- Application Information
AI Technical Summary
Problems solved by technology
Method used
Image
Examples
Embodiment 1
[0049] Such as figure 2 As shown, the host 100 is, from top to bottom, an upper body cover 1 , a filter element body 4 , a middle plate 11 , and a base 25 .
[0050] The filter element body 4 is a square frame structure, which is divided into a clear liquid tank located at the upper part and a filter element tank located at the lower part. The upper cover plate 1 of the main body is installed on the end face of the clear liquid tank of the filter element body 4 through the hexagon socket head bolt 2, and the joint is provided with O-shaped sealing ring 3, a clear liquid outlet 39 is provided on one side of the clear liquid tank, an inner wall shoulder flange is provided at the transition between the clear liquid tank and the filter element tank, and the inner pressure plate 5 of the body is installed on the inner wall shoulder flange through the inner hexagonal bolt 6 Above, the clear liquid tank is separated from the filter core tank, and a number of through grooves are prov...
PUM
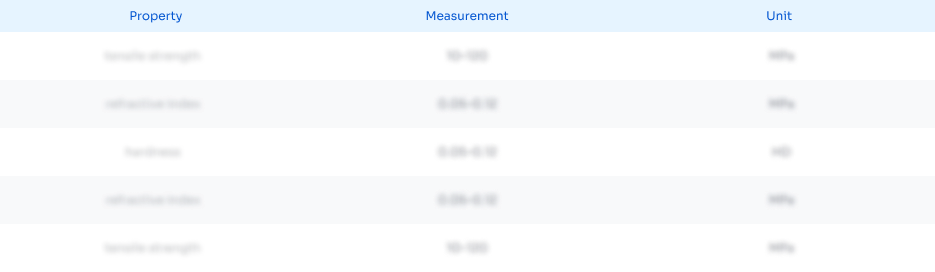
Abstract
Description
Claims
Application Information

- R&D
- Intellectual Property
- Life Sciences
- Materials
- Tech Scout
- Unparalleled Data Quality
- Higher Quality Content
- 60% Fewer Hallucinations
Browse by: Latest US Patents, China's latest patents, Technical Efficacy Thesaurus, Application Domain, Technology Topic, Popular Technical Reports.
© 2025 PatSnap. All rights reserved.Legal|Privacy policy|Modern Slavery Act Transparency Statement|Sitemap|About US| Contact US: help@patsnap.com