Shaft type connecting rod transmission system and opposed piston engine
A connecting rod transmission, opposed piston technology, applied in the direction of transmission, machine/engine, mechanical equipment, etc., can solve the problems of complex limit mechanism, mechanical wear and noise, left and right baffle impact, etc., to simplify the transmission system and Gas distribution system, reducing mechanical wear and noise, and the effect of compact overall structure
- Summary
- Abstract
- Description
- Claims
- Application Information
AI Technical Summary
Problems solved by technology
Method used
Image
Examples
Embodiment 1
[0042] Figure 6 to Figure 9 Shown is a two-stroke dual opposed piston engine. Taking the axis of the main shaft 10 as the reference center, the piston close to the axis is called the "inner piston", and the piston farther from the axis than the "inner piston" is called the "outer piston". Similarly, the axial connecting rod fixedly connected to the "inner piston" is called the "inner axial connecting rod", and the axial connecting rod fixedly connected to the "outer piston" is called the "outer frame-shaped axial connecting rod".
[0043] Reference Image 6 , Figure 7 The opposed-piston engine of the present invention includes at least a pair of linear reciprocating units arranged on the planes on both sides of the axis of the main shaft 10, and the linear reciprocating body A includes an inner piston 51a and an outer piston 51b arranged in the cylinder 50. The axial connecting rod 40 includes an inner axial connecting rod 40a whose inner end is fixedly connected to the inner ...
Embodiment 2
[0054] Picture 9 with Picture 10 Shown is a four-stroke opposed-piston engine, which includes at least a pair of linear reciprocating units arranged on two planes of the axis of the main shaft 10, and the linear reciprocating body A is a piston 51 arranged in a cylinder 50. The axial connecting rod 40 is an inner axial connecting rod 40a whose outer end is fixedly connected to the piston 51, the push-pull frame 20 is a first push-pull frame 20a, and the inner end of the inner axial link 40a is connected to the first push-pull frame One side of 20a is fixedly connected. An intake valve 57 and an exhaust valve 58 are provided on the outer end cover 52b of the cylinder 50. A timing system is provided between the main shaft 10 and the intake valve 57 and the exhaust valve 58. The timing system operates in a four-stroke mode. Match gas.
[0055] The timing system can adopt a variety of conventional devices, such as belt timing system, chain timing system, Picture 10 What is shown ...
Embodiment 3
[0062] Picture 11 with Picture 12 Shown is a two-stroke opposed-piston engine. The opposed-piston engine includes at least a pair of linear reciprocating units arranged on the planes on both sides of the axis of the main shaft 10, and the linear reciprocating body A is arranged in the cylinder 50 Piston 51. The axial connecting rod 40 is an inner axial connecting rod 40a whose outer end is fixedly connected to the piston 51, and the push-pull frame 20 is a first push-pull frame 20a. The inner end of the inner shaft connecting rod 40a is fixedly connected to one side of the first push-pull frame 20a, an exhaust valve 58 is provided on the outer end cover 52b of the cylinder 50, and a timing system is provided between the main shaft 10 and the exhaust valve 58 The timing system cooperates with the air intake port 55 controlled by the piston stroke to perform gas distribution in a two-stroke working mode.
[0063] Reference Picture 12 The timing system includes an outer frame-sh...
PUM
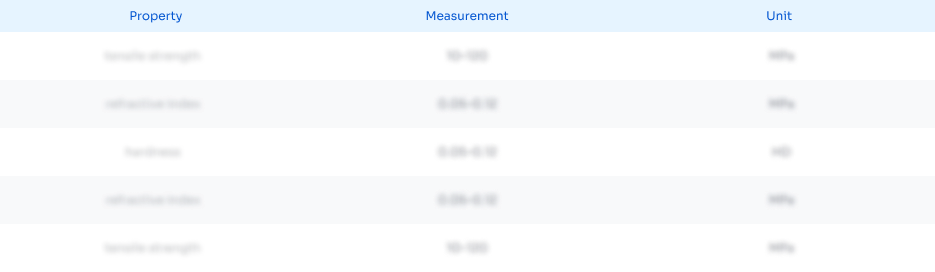
Abstract
Description
Claims
Application Information

- R&D
- Intellectual Property
- Life Sciences
- Materials
- Tech Scout
- Unparalleled Data Quality
- Higher Quality Content
- 60% Fewer Hallucinations
Browse by: Latest US Patents, China's latest patents, Technical Efficacy Thesaurus, Application Domain, Technology Topic, Popular Technical Reports.
© 2025 PatSnap. All rights reserved.Legal|Privacy policy|Modern Slavery Act Transparency Statement|Sitemap|About US| Contact US: help@patsnap.com