Method for purifying acetone from waste residue and waste water produced in ketene dimmer production process
A production process and technology of diketene, which are applied in the separation/purification of carboxylic acid compounds, the separation/purification of carbonyl compounds, and the preparation of carbonyl compounds by hydrolysis, can solve the problems of low purity and low yield of recovered acetone, and achieve increased output and savings The effect of increasing production cost and content
- Summary
- Abstract
- Description
- Claims
- Application Information
AI Technical Summary
Problems solved by technology
Method used
Examples
Embodiment 1
[0012] Put 800kg of acetic acid with a content of 46% into the hydrolysis kettle, then heat up the hydrolysis kettle, and control the steam pressure at about 0.2MPa. When you see reflux acetic acid in the reflux mirror (temperature 80°C-95°C), turn off the steam and start Slowly add the residue diluent (about 1.8t) dropwise. During the dropwise addition, the pressure of the hydrolysis tank is controlled at 2-5KPa, and the dropwise addition time is controlled at about 2h. After the dropwise addition, keep warm for 30-60 minutes, and keep the kettle temperature at 90-95°C to make it fully react. Gas phase through 50m 2 The vertical heat exchanger cools down to 56-65 ℃, and then passes through 40m 2 The plate is cooled by shallow cold brine to condense the acetone, and the liquid acetone is separated by the gas-liquid separator and sent to the crude acetone tank. The production time of each kettle is about 8 hours, and the production content of about 65% is about 2 tons of acet...
Embodiment 2
[0016] Put 900kg of acetic acid with a content of 45%-50% into the hydrolysis kettle, then heat up the hydrolysis kettle, and control the steam pressure at about 0.2MPa. When you see reflux acetic acid in the reflux mirror (temperature 80°C-95°C), close the Steam, began to slowly drop the residue dilution (about 2t). During the dropwise addition, the pressure of the hydrolysis tank is controlled at 2-5KPa, and the dropwise addition time is controlled at about 2h. After the dropwise addition, keep warm for 30-60 minutes, and keep the kettle temperature at 90-95°C to make it fully react. Gas phase through 50m 2 The vertical heat exchanger cools down to 56-65 ℃, and then passes through 40m 2 The plate is cooled by shallow cold brine to condense the acetone, and the liquid acetone is separated by the gas-liquid separator and sent to the crude acetone tank. The production time of each kettle is about 8 hours, and the yield of acetone with a content of about 65% is about 2.2 tons....
PUM
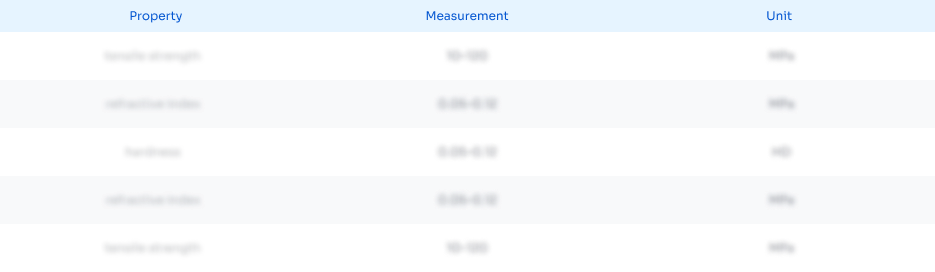
Abstract
Description
Claims
Application Information

- Generate Ideas
- Intellectual Property
- Life Sciences
- Materials
- Tech Scout
- Unparalleled Data Quality
- Higher Quality Content
- 60% Fewer Hallucinations
Browse by: Latest US Patents, China's latest patents, Technical Efficacy Thesaurus, Application Domain, Technology Topic, Popular Technical Reports.
© 2025 PatSnap. All rights reserved.Legal|Privacy policy|Modern Slavery Act Transparency Statement|Sitemap|About US| Contact US: help@patsnap.com