Method for repairing converter lining
A converter lining and converter technology, which is applied in the field of iron and steel metallurgy, can solve the problems of limited repairing of the furnace lining, poor safety, high labor intensity, etc., and achieve the effects of shortening the repairing time, not easy to fall off, and improving the repairing effect.
- Summary
- Abstract
- Description
- Claims
- Application Information
AI Technical Summary
Problems solved by technology
Method used
Examples
Embodiment 1
[0016] The estimated slag of the 180-ton converter is 16-20 tons (calculated on the basis of an average of 18 tons). Add 10kg / t of magnesium oxide particles to slag, add 120kg of magnesium oxide particles, add 96kg of dolomite according to the dolomite dosage of 8kg / t slag, temper the slag, and blow it evenly with nitrogen. Add 2 tons of magnesia-carbon bricks with a physical size of 300mm×200mm×70mm into it for sintering. The slag temperature is controlled between 1270±30°C. Tilt the converter back and forth to make the slag and magnesia-carbon bricks fully mixed evenly, and then tilt the converter at an angle The temperature is controlled at 106.7°, and the sintering time is 80 minutes to quickly repair the large surface of the furnace lining. After the repair, the carbon bricks are firmly bonded to the lining of the converter without falling off.
[0017] Compared with the traditional method of pasting magnesia-carbon bricks, this method saves at least 40 minutes of time f...
Embodiment 2
[0019] The estimated slag of a 180-ton converter is 13-16 tons. After tapping, 10 tons of slag will be set aside according to the mass ratio of slag to magnesia-carbon bricks (1 ton) to be added at 10:1. Add 30kg of dolomite to 3kg / t slag of dolomite, add 50kg of magnesium oxide particles to 5kg / t slag of magnesium oxide particles, temper the slag, and blow it evenly with nitrogen. Add 1 ton of magnesia-carbon bricks with a physical size of 300mm×200mm×70mm, and repeatedly tilt the converter back and forth to make the slag and magnesia-carbon bricks fully uniform, and then control the tilting angle of the converter at -99.3° to quickly repair the small surface of the furnace lining. The sintering time was 45 minutes. The temperature is controlled at 1180±30°C. After the repair, the carbon bricks are firmly bonded to the lining of the converter without falling off.
[0020] This method saves at least 75 minutes of time compared with the traditional magnesium-carbon conversion...
Embodiment 3
[0022] The estimated slag of a 180-ton converter is 15-18 tons. After tapping, 12 tons of slag will be set aside according to the mass ratio of slag to magnesia-carbon bricks (1.5 tons) to be added at 8:1. Add 60kg of dolomite to 5kg / t slag of dolomite, and 84kg of magnesia particles to 7kg / t slag of magnesium oxide particles to temper the slag and blow it evenly with nitrogen. Add 1.5 tons of magnesia-carbon bricks with a physical size of 300mm×200mm×70mm, and repeatedly tilt the converter back and forth to make the slag and magnesia-carbon bricks fully uniform, and then control the tilting angle of the converter at 103.6° to quickly repair the large surface of the furnace lining and sinter The time is 60 minutes. The temperature is controlled at 1250±30°C. After the repair, the carbon bricks are firmly bonded to the lining of the converter without falling off.
[0023] Compared with the traditional method of pasting magnesia-carbon bricks, this method saves 60 minutes of q...
PUM
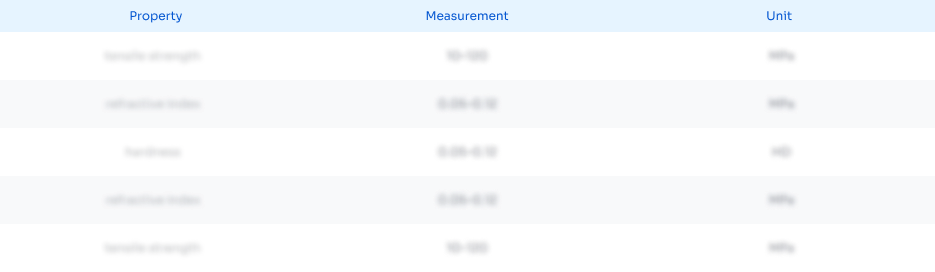
Abstract
Description
Claims
Application Information

- R&D Engineer
- R&D Manager
- IP Professional
- Industry Leading Data Capabilities
- Powerful AI technology
- Patent DNA Extraction
Browse by: Latest US Patents, China's latest patents, Technical Efficacy Thesaurus, Application Domain, Technology Topic, Popular Technical Reports.
© 2024 PatSnap. All rights reserved.Legal|Privacy policy|Modern Slavery Act Transparency Statement|Sitemap|About US| Contact US: help@patsnap.com