Composite membrane, preparation method of composite membrane and mold for preparing easy-to-tear strip
A technology of composite film and easy-tearing thread, which is applied in the field of packaging materials, can solve problems such as poor tearability, affecting use and appearance, and achieve the effect of improving bonding strength, increasing bonding performance, and good bonding
- Summary
- Abstract
- Description
- Claims
- Application Information
AI Technical Summary
Problems solved by technology
Method used
Image
Examples
Embodiment 1
[0045] The composite film of this embodiment includes a paper layer 2, an aluminum foil layer 4 and an inner layer 6 bonded in sequence, and the paper layer 2 is provided with any form of easy-tear structure described above. Wherein, the inner layer is made of 40wt% styrene-butadiene copolymer, 25wt% HDPE and 35wt% LDPE mixed homogeneously and then blow-molded at 165°C.
[0046] Such as figure 2 Shown, the preparation method of the composite membrane of the present application is,
[0047] (1) Make easy-tear lines on the paper layer.
[0048] (2) Coat one side of the aluminum foil layer with an adhesive, and dry it in a three-stage oven at 70°C, 75°C, and 80°C successively at a speed of 200 m / min to obtain the first adhesive layer 3. Under the condition of 50°C, the paper layer and the first adhesive layer are hot-compressed together.
[0049] (3) Coat the other side of the aluminum foil layer with an adhesive, and dry it in a three-stage oven at 50°C, 60°C, and 70°C succe...
Embodiment 2
[0052] The composite film of this embodiment includes a paper layer 2, an aluminum foil layer 4 and an inner layer 6 bonded in sequence, and the paper layer 2 is provided with any form of easy-tear structure described above. Wherein, the inner layer is made of 40wt% styrene-butadiene copolymer, 15wt% HDPE and 45wt% LDPE mixed uniformly, and then blow-molded at 165°C.
[0053] Such as figure 2 Shown, the preparation method of the composite membrane of the present application is,
[0054] (1) Make easy-tear lines on the paper layer.
[0055] (2) Coat one side of the aluminum foil layer with an adhesive, and dry it in a three-stage oven at 75°C, 85°C, and 95°C successively at a speed of 190 m / min to obtain the first adhesive layer 3. Under the condition of 70°C, the paper layer and the first adhesive layer are hot-compressed together.
[0056] (3) Coat the other side of the aluminum foil layer with an adhesive, and dry it in a three-stage oven at 60°C, 70°C, and 80°C successi...
Embodiment 3
[0060] The composite film of this embodiment includes a paper layer 2, an aluminum foil layer 4 and an inner layer 6 bonded in sequence, and the paper layer 2 is provided with any form of easy-tear structure described above. Wherein, the inner layer is made of 30wt% styrene-butadiene copolymer, 20wt% HDPE and 50wt% LDPE mixed uniformly and then blow-molded at 165°C.
[0061] Such as figure 2 Shown, the preparation method of the composite membrane of the present application is,
[0062] (1) Printing on the paper layer.
[0063] (2) Make easy-tear lines on the paper layer.
[0064] (3) Coat one side of the aluminum foil layer with an adhesive, and dry it in a three-stage oven at 72°C, 80°C, and 90°C successively at a speed of 180 m / min to obtain the first adhesive layer 3. Under the condition of 60°C, the paper layer and the first adhesive layer are heat-compressed together.
[0065] (4) Coat the other side of the aluminum foil layer with an adhesive, and dry it in a three-...
PUM
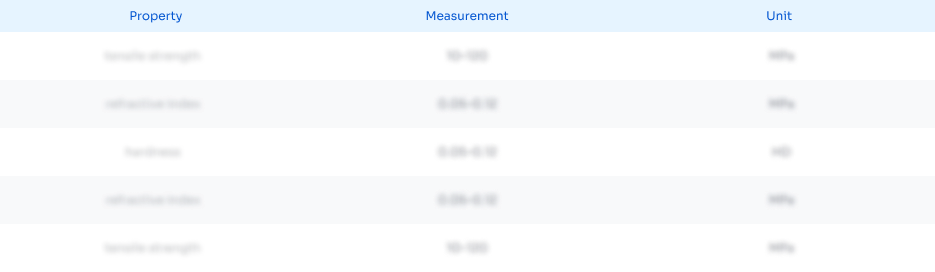
Abstract
Description
Claims
Application Information

- R&D
- Intellectual Property
- Life Sciences
- Materials
- Tech Scout
- Unparalleled Data Quality
- Higher Quality Content
- 60% Fewer Hallucinations
Browse by: Latest US Patents, China's latest patents, Technical Efficacy Thesaurus, Application Domain, Technology Topic, Popular Technical Reports.
© 2025 PatSnap. All rights reserved.Legal|Privacy policy|Modern Slavery Act Transparency Statement|Sitemap|About US| Contact US: help@patsnap.com