Electric furnace smelting method of steel for welding wire
An electric furnace smelting and welding wire technology, which is applied in the field of iron and steel metallurgy, can solve the problems that dephosphorization, deoxidation and desulfurization reactions are difficult to control, it is difficult to smelt high-purity welding wire steel, and the desulfurization reaction is affected, so as to achieve low production costs and guarantee Fluidity, the effect of improving the dephosphorization rate
- Summary
- Abstract
- Description
- Claims
- Application Information
AI Technical Summary
Problems solved by technology
Method used
Examples
Embodiment 1
[0024] During electric furnace smelting, the furnace material structure includes molten iron and scrap steel, of which the amount of molten iron is 85t, the amount of high-quality scrap steel is 27t, and the ratio of molten iron is 76%. Within minutes, the principle of feeding in batches is adopted, the total amount of lime added is 2780kg, the time to start slag flow is 16 minutes after blowing, the slag alkalinity is 2.1 during slag flow, and the T.Fe content in slag is 30%; Minutes, the temperature of the molten pool is 1534°C, the phosphorus content of the molten pool is 0.0162%; the carbon content in the molten pool is 0.043%, the phosphorus content is 0.0056%, and the steel is tapped at 1607°C; the tapping amount is 1% of the total tapping amount At 17%, alloy and slag are added to the ladle in the order of "ferrosilicon→low-carbon ferromanganese→lime→fluorite". 320kg.
[0025] During ladle refining, lime, fluorite and calcium carbide are added in batches to adjust the ...
Embodiment 2
[0029] During electric furnace smelting, the charge structure includes molten iron and scrap steel, of which the amount of molten iron is 87t, the amount of high-quality scrap steel is 25t, and the ratio of molten iron is 78%. Within minutes, the principle of batch feeding is adopted, the total amount of lime added is 1850kg, the time to start slag flow is 18 minutes after blowing, the slag alkalinity during slag flow is 2.2, and the T.Fe content in slag is 28%; Minutes, the molten pool temperature is 1550°C, the phosphorus content in the molten pool is 0.0186%; the carbon content in the molten pool is 0.055%, the phosphorus content is 0.0052%, and the steel is tapped at a temperature of 1614°C; the tapping amount is 1% of the total tapping amount At 18%, alloy and slag are added to the ladle in the order of "ferrosilicon→low-carbon ferromanganese→lime→fluorite". 300kg.
[0030] During ladle refining, according to the deoxidation of slag and molten steel, lime, fluorite and c...
Embodiment 3
[0034] During electric furnace smelting, the furnace material structure includes molten iron and scrap steel, of which the amount of molten iron is 88t, the amount of high-quality scrap steel is 24t, and the ratio of molten iron is 79%. Within minutes, the principle of batch feeding is adopted, the total amount of lime added is 2440kg, the time to start slag flow is 18 minutes after blowing, the slag alkalinity is 2.0 during slag flow, and the T.Fe content in slag is 27%; Minutes, the molten pool temperature is 1527°C, the phosphorus content in the molten pool is 0.0173%; the carbon content in the molten pool is 0.048%, the phosphorus content is 0.0050%, and the steel is tapped at a temperature of 1619°C; the tapping amount is 1% of the total tapping amount At 17%, alloy and slag are added to the ladle in the order of "ferrosilicon→low-carbon ferromanganese→lime→fluorite". 308kg.
[0035] During ladle refining, according to the deoxidation of slag and molten steel, lime, fluo...
PUM
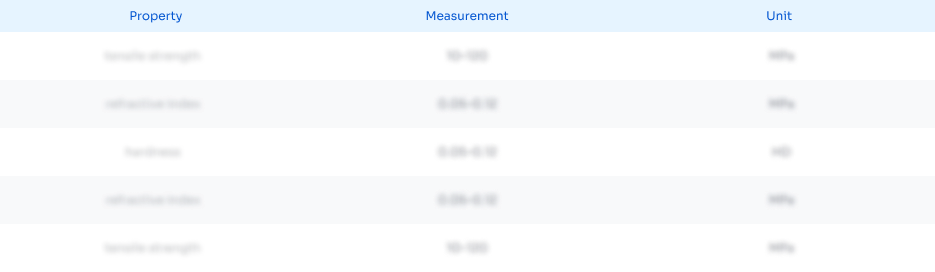
Abstract
Description
Claims
Application Information

- Generate Ideas
- Intellectual Property
- Life Sciences
- Materials
- Tech Scout
- Unparalleled Data Quality
- Higher Quality Content
- 60% Fewer Hallucinations
Browse by: Latest US Patents, China's latest patents, Technical Efficacy Thesaurus, Application Domain, Technology Topic, Popular Technical Reports.
© 2025 PatSnap. All rights reserved.Legal|Privacy policy|Modern Slavery Act Transparency Statement|Sitemap|About US| Contact US: help@patsnap.com