Low-cost efficient dephosphorization smelting process for electric arc furnace
A high-efficiency dephosphorization and electric arc furnace technology, applied in the direction of electric furnace, process efficiency improvement, furnace, etc., can solve the problems of dephosphorization oxygen position, alkalinity, temperature theory demand contradiction, etc., to enhance the process matching ability and improve dephosphorization The effect of reducing the efficiency and process cost
- Summary
- Abstract
- Description
- Claims
- Application Information
AI Technical Summary
Problems solved by technology
Method used
Image
Examples
Embodiment 1
[0038] Take a 100-ton ultra-high power electric arc furnace with 5 furnace wall oxygen lances as an example:
[0039] (1) Put 60 tons of ferronickel, 15 tons of steel scrap, 15 tons of iron oxide balls, and 7 tons of lime into the material basket in sequence: ① 10 tons of nickel iron, ② 5 tons of iron oxide balls, 2 tons of lime, ③ 20 tons of ferronickel, ④ 5 tons of iron oxide balls, 3 tons of lime, ⑤ 30 tons of nickel iron, ⑥ 5 tons of iron oxide balls, 2 tons of lime, ⑦ 15 tons of steel scrap.
[0040] (2) After the raw materials in the material basket are loaded into the electric arc furnace, the electricity is smelted, and the furnace wall gun is fully opened. After the molten pool appears, the furnace door gun blows oxygen, and the oxygen supply intensity is controlled at 1.5Nm 3 / min.t steel, after the slag surface in the furnace is basically free of solid alloys, take a steel sample to test the composition, and add 200kg of fluorite depending on the fluidity of the sl...
Embodiment 2
[0045] Take a 60-ton ultra-high power electric arc furnace with 3 furnace wall oxygen lances as an example:
[0046](1) Put 35 tons of ferronickel, 3 tons of stainless steel scrap, 8 tons of iron oxide balls, and 4 tons of lime into the material basket in order of hierarchy: ① 2 tons of iron oxide balls, 1 ton of lime, ② 15 tons of nickel Iron, ③ 4 tons of iron oxide balls, 2 tons of lime, ④ 20 tons of ferronickel, ⑤ 2 tons of iron oxide balls, 1 ton of lime, ⑥ 3 tons of steel scrap.
[0047] (2) After the raw materials in the material basket are loaded into the electric arc furnace, the electricity is smelted, and the furnace wall gun is fully opened. After the molten pool appears, the furnace door gun blows oxygen, and the oxygen supply intensity is 1.2Nm 3 / min.t steel, the oxygen supply of the furnace door gun reaches about 1000Nm 3 Stop blowing oxygen. Before the solid alloy in the furnace is completely melted for 2~3 minutes, use a professional sampler to take a sampl...
PUM
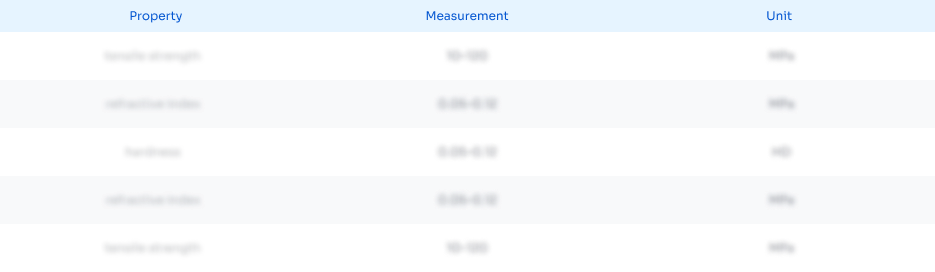
Abstract
Description
Claims
Application Information

- R&D
- Intellectual Property
- Life Sciences
- Materials
- Tech Scout
- Unparalleled Data Quality
- Higher Quality Content
- 60% Fewer Hallucinations
Browse by: Latest US Patents, China's latest patents, Technical Efficacy Thesaurus, Application Domain, Technology Topic, Popular Technical Reports.
© 2025 PatSnap. All rights reserved.Legal|Privacy policy|Modern Slavery Act Transparency Statement|Sitemap|About US| Contact US: help@patsnap.com