Slag melting agent and preparation method thereof and semi-steel steelmaking method adopting slag melting agent
A technology of slag-removing agent and molten steel, which is applied in the field of semi-steel steelmaking and semi-steel steelmaking in converters. It can solve the problems of reducing the amount of alloyed manganese, sticking guns, and difficulties in dephosphorization, and achieve the effect of reducing the amount of use.
- Summary
- Abstract
- Description
- Claims
- Application Information
AI Technical Summary
Problems solved by technology
Method used
Image
Examples
Embodiment 1
[0050] The slag-removing agent is mainly prepared from the following raw materials according to the percentage by weight of each raw material:
[0051]
[0052] Among them, the main components and contents of manganese ore powder, vanadium extraction tailings, iron oxide scale, lime powder, bentonite and binder are shown in Table 3:
[0053] table 3
[0054] Element
TF
SiO 2
CaO
Al 2 o 3
MnO
Impurities
[0055]
(%)
(%)
(%)
(%)
(%)
(%)
Manganese ore powder
12.79
39.96
7.60
7.65
9.71
margin
38.43
15.65
3.67
1.66
6.35
margin
Iron oxide scale
70.00
/
/
/
/
margin
lime powder
/
4.00
78.00
/
/
margin
2.20
59.20
3.44
/
/
margin
binder
/
/
/
/
/
/
[0056] The preparatio...
Embodiment 2
[0071] The slag-removing agent is mainly prepared from the following raw materials according to the percentage by weight of each raw material:
[0072]
[0073] Among them, the contents of the main components of manganese ore powder, vanadium extraction tailings, iron oxide scale, lime powder, bentonite and binder are shown in Table 3.
[0074] The preparation method of the slagging agent is as follows: crush manganese ore powder and lime powder until the particle size is less than 3mm. Mix 460kg of manganese ore powder, 200kg of vanadium extraction tailings, 100kg of bentonite, 130kg of iron oxide scale, 80kg of lime powder and 30kg of binder, mix them evenly, press them into balls, transport them to the baking equipment by belt, and dry them for 2 hours. The weight percentage of water is less than 3%, and the slag balls are obtained.
[0075] After the slag ball falls freely from a height of 2 meters to the cement floor, the weight of the powder surface (particle size < ...
Embodiment 3
[0087] The slag-removing agent is mainly prepared from the following raw materials according to the percentage by weight of each raw material:
[0088]
[0089] Among them, the contents of the main components of manganese ore powder, vanadium extraction tailings, iron oxide scale, lime powder, bentonite and binder are shown in Table 3.
[0090] The preparation method of the slagging agent is as follows: crush manganese ore powder and lime powder until the particle size is less than 3mm. Mix 450kg of manganese ore powder, 300kg of vanadium extraction tailings, 100kg of bentonite, 70kg of iron oxide scale, 55kg of lime powder and 25kg of binder, mix them evenly, press them into balls, transport them to the baking equipment by belt, and dry them for 2.5 hours. The weight percentage of water is less than 3%, and the slag balls are obtained.
[0091] After the slag ball falls freely from a height of 2 meters to the cement floor, the weight of the powder surface (particle size <...
PUM
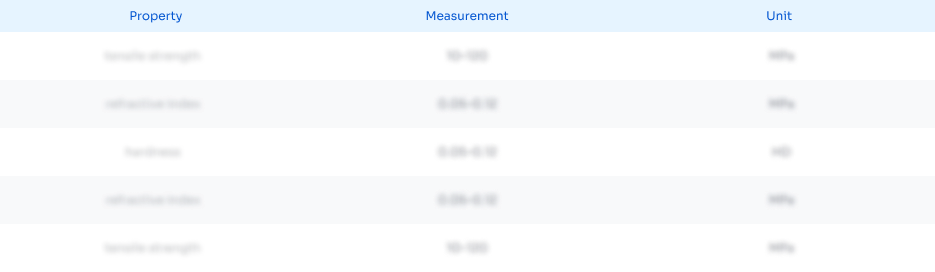
Abstract
Description
Claims
Application Information

- R&D
- Intellectual Property
- Life Sciences
- Materials
- Tech Scout
- Unparalleled Data Quality
- Higher Quality Content
- 60% Fewer Hallucinations
Browse by: Latest US Patents, China's latest patents, Technical Efficacy Thesaurus, Application Domain, Technology Topic, Popular Technical Reports.
© 2025 PatSnap. All rights reserved.Legal|Privacy policy|Modern Slavery Act Transparency Statement|Sitemap|About US| Contact US: help@patsnap.com