Punch forming method and punch forming die for corrugated metal foil
A stamping forming and mold technology, which is applied in the metal corrugated foil stamping forming method and stamping forming mold field, can solve the corrugated foil size and mechanical properties are not good, it is difficult to achieve high amplitude forming, high bending ratio and other problems, Achieve good dimensional consistency, solve the effect of easy fracture and stable mechanical properties
- Summary
- Abstract
- Description
- Claims
- Application Information
AI Technical Summary
Problems solved by technology
Method used
Image
Examples
Embodiment Construction
[0029] The invention provides a metal corrugated foil stamping forming method and a stamping forming mold thereof. In order to make the object, technical solution and effect of the present invention more clear and definite, the present invention will be further described in detail below with reference to the accompanying drawings and examples. It should be understood that the specific embodiments described here are only used to explain the present invention, not to limit the present invention.
[0030] Such as figure 1 Shown is a metal corrugated foil stamping die according to a specific embodiment of the present invention.
[0031] The stamping mold shown includes: an upper rack die 10 and a lower rack die 20 .
[0032] Among them, such as figure 2 and image 3 As shown, the upper rack mold 10 includes an upper forming tooth seat 100, an upper forming tooth 110 disposed on the upper forming tooth seat, and an upper shaping tooth rack 300 movable relative to the upper for...
PUM
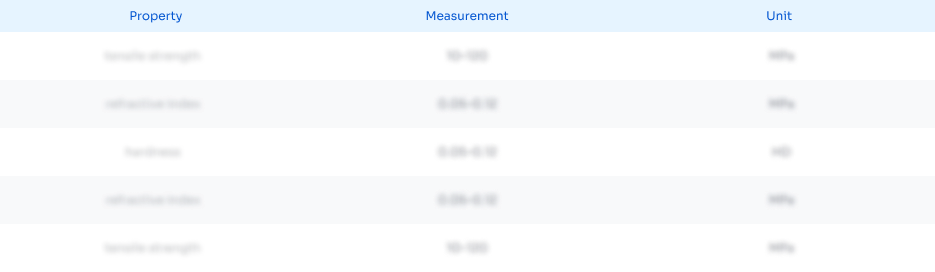
Abstract
Description
Claims
Application Information

- R&D
- Intellectual Property
- Life Sciences
- Materials
- Tech Scout
- Unparalleled Data Quality
- Higher Quality Content
- 60% Fewer Hallucinations
Browse by: Latest US Patents, China's latest patents, Technical Efficacy Thesaurus, Application Domain, Technology Topic, Popular Technical Reports.
© 2025 PatSnap. All rights reserved.Legal|Privacy policy|Modern Slavery Act Transparency Statement|Sitemap|About US| Contact US: help@patsnap.com