Collecting pipe machining process and forming equipment thereof
A technology of processing, forming and processing technology, which is applied in the field of collecting tube processing technology and its forming equipment, and can solve the problems of uneven spacing, low stamping efficiency, and affecting the clamping of louver corrugated heat sinks, etc.
- Summary
- Abstract
- Description
- Claims
- Application Information
AI Technical Summary
Problems solved by technology
Method used
Image
Examples
Embodiment Construction
[0039] The present invention will be further described below in conjunction with the accompanying drawings:
[0040] Referring to the accompanying drawings: the processing technology of this header is characterized by the following steps:
[0041] A. Loading: Insert the steel pipe 11-1 into the cylindrical rod 3a;
[0042] B. Clamping correction: first start the power switch 9, part of the program of the PLC controller 8 is activated, the PLC controller 8 controls the second cylinder 4f to drive the sliding block 4a to move, so that the first sliding block 4b is located above the cylindrical rod 3a, and then Manually move the end face of the steel pipe 11-1 to fit the end face of the first slider 4b, and then twist the screw block 4e used to adjust the movement of the first slider 4b, so as to adjust the steel pipe 11-1 and the punching piece 2a1- The relative position between 6 (the same batch of products only need to be adjusted once), then press the program switch 10, the ...
PUM
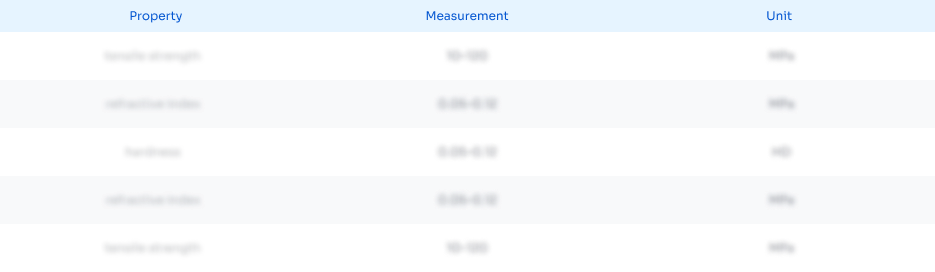
Abstract
Description
Claims
Application Information

- R&D
- Intellectual Property
- Life Sciences
- Materials
- Tech Scout
- Unparalleled Data Quality
- Higher Quality Content
- 60% Fewer Hallucinations
Browse by: Latest US Patents, China's latest patents, Technical Efficacy Thesaurus, Application Domain, Technology Topic, Popular Technical Reports.
© 2025 PatSnap. All rights reserved.Legal|Privacy policy|Modern Slavery Act Transparency Statement|Sitemap|About US| Contact US: help@patsnap.com