Adjusting method of built-in mechanical on-line dynamic balancing system of main shaft
An adjustment method, a mechanical technology, applied in the static/dynamic balance test, general control system, control/adjustment system, etc., can solve the problems of spindle dynamic unbalance, affecting the spindle rotation accuracy, instability, etc., to improve the rotation speed Accuracy, practical adjustment method, full-featured effect
- Summary
- Abstract
- Description
- Claims
- Application Information
AI Technical Summary
Problems solved by technology
Method used
Image
Examples
Embodiment
[0056] Example: such as figure 1 As shown, the adjustment method of the present invention comprises the following steps:
[0057] Step 1: Install an online dynamic balancing system, such as Figure 8-Figure 11 shown;
[0058] Step 1.1: Place the dynamic balancing device in the inner hole of the main shaft 19, fix the expansion ring 1 firmly and fix the dynamic balancing device in the inner cavity of the main shaft 19, and ensure that the dynamic balancing device is concentric with the rotation center of the main shaft 19;
[0059] Step 1.2: Fix the two acceleration sensors I18 and II22 on the main shaft sleeve 20 respectively, the plane formed by the center line of the two acceleration sensors and the axis of the main shaft 19 is perpendicular to the horizontal plane, and measure the distance between the acceleration sensor and the main shaft sleeve 20 - a fixed point The distance is l 2 , l 6 ;
[0060] Step 1.3: install the phase sensor 25 horizontally, set it at the ce...
PUM
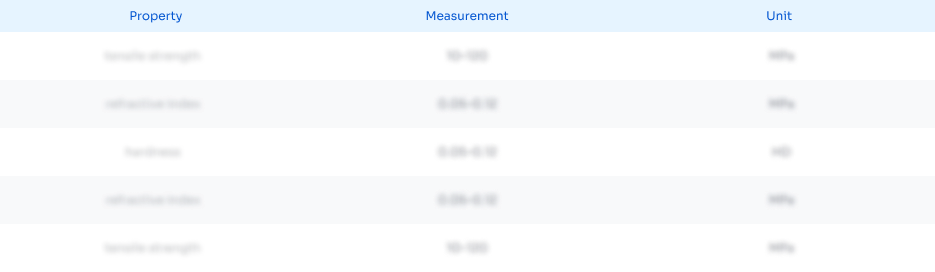
Abstract
Description
Claims
Application Information

- R&D
- Intellectual Property
- Life Sciences
- Materials
- Tech Scout
- Unparalleled Data Quality
- Higher Quality Content
- 60% Fewer Hallucinations
Browse by: Latest US Patents, China's latest patents, Technical Efficacy Thesaurus, Application Domain, Technology Topic, Popular Technical Reports.
© 2025 PatSnap. All rights reserved.Legal|Privacy policy|Modern Slavery Act Transparency Statement|Sitemap|About US| Contact US: help@patsnap.com