Treatment and utilization method for sintering flue gas
A technology of sintering flue gas and flue gas, which is applied in the field of metallurgy, can solve the problems of high operating cost, difficulty in using desulfurization products and denitrification products, etc., and achieve the effect of less increase in sulfur and nitrogen content
- Summary
- Abstract
- Description
- Claims
- Application Information
AI Technical Summary
Problems solved by technology
Method used
Image
Examples
Embodiment 1
[0053] After the sintering flue gas passes through the electrostatic precipitator, the temperature is 150°C. After passing through the main exhaust fan, it is sent to the hot blast stove through the gas pipeline. The flow rate is 5000 cubic meters per minute, and the air replacement rate is 100%, of which SO 2 Content 1000mg / m 3 , nitrogen oxide concentration 200mg / m 3 ; heated to 1200 ℃ in the hot blast furnace, blown into the blast furnace by the blower through the tuyere of the blast furnace; in the blast furnace, the sintering flue gas and the blast furnace charge undergo a chemical reaction, sulfur dioxide is reduced and enters molten iron and slag, nitrogen oxides are reduced and enter molten iron and Blast furnace gas, dioxin and furan decompose at high temperature, carbon dioxide reacts with carbon in the blast furnace to generate carbon monoxide, which becomes a reducing agent or enters blast furnace gas, oxygen reacts with carbon to generate carbon monoxide, and rele...
Embodiment 2
[0055] After the sintering flue gas passes through the bag dust removal, the temperature is 170°C, after passing through the main exhaust fan, it is sent to the hot blast stove through the gas pipeline, the flow rate is 4000 cubic meters per minute, and the air replacement rate is 80%, of which SO 2 Content 2000mg / m 3 , nitrogen oxide concentration 400mg / m 3 ;Heated to 1250°C in the hot blast furnace, blown into the blast furnace by the blower through the blast furnace tuyere; in the blast furnace, the sintering flue gas and the blast furnace charge undergo a chemical reaction, sulfur dioxide is reduced and enters molten iron and slag, nitrogen oxides are reduced and enter molten iron and Blast furnace gas, dioxin and furan decompose at high temperature, carbon dioxide reacts with carbon in the blast furnace to generate carbon monoxide, which becomes a reducing agent or enters blast furnace gas, oxygen reacts with carbon to generate carbon monoxide, and releases reaction heat....
Embodiment 3
[0057] After the sintering flue gas passes through the bag dust removal, the temperature is 200°C, after passing through the main exhaust fan, it is sent to the hot blast stove through the gas pipeline, the flow rate is 3000 cubic meters per minute, and the air replacement rate is 60%, of which SO 2 Content 3000mg / m 3 , nitrogen oxide concentration 600mg / m 3 ;Heated to 1250°C in the hot blast furnace, blown into the blast furnace by the blower through the blast furnace tuyere; in the blast furnace, the sintering flue gas and the blast furnace charge undergo a chemical reaction, sulfur dioxide is reduced and enters molten iron and slag, nitrogen oxides are reduced and enter molten iron and Blast furnace gas, dioxin and furan decompose at high temperature, carbon dioxide reacts with carbon in the blast furnace to generate carbon monoxide, which becomes a reducing agent or enters blast furnace gas, oxygen reacts with carbon to generate carbon monoxide, and releases reaction heat....
PUM
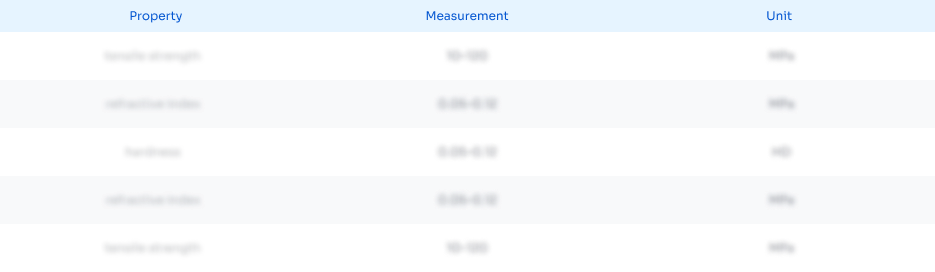
Abstract
Description
Claims
Application Information

- Generate Ideas
- Intellectual Property
- Life Sciences
- Materials
- Tech Scout
- Unparalleled Data Quality
- Higher Quality Content
- 60% Fewer Hallucinations
Browse by: Latest US Patents, China's latest patents, Technical Efficacy Thesaurus, Application Domain, Technology Topic, Popular Technical Reports.
© 2025 PatSnap. All rights reserved.Legal|Privacy policy|Modern Slavery Act Transparency Statement|Sitemap|About US| Contact US: help@patsnap.com