Contact thermal resistance modeling method considering elasticoplastic deformation of micro-bulge and thermal resistance of air medium
A technology of elastic-plastic deformation and contact thermal resistance, which is applied in special data processing applications, instruments, electrical digital data processing, etc., can solve the problems of not considering the thermal resistance of the gap air medium, not considering the elastic-plastic deformation of asperities, etc.
- Summary
- Abstract
- Description
- Claims
- Application Information
AI Technical Summary
Problems solved by technology
Method used
Image
Examples
Embodiment Construction
[0015] The present invention implements a contact thermal resistance modeling method considering the elastic-plastic deformation of the asperity and the thermal resistance of the air medium in the gap. The implementation of the present invention will be described in detail below in conjunction with the accompanying drawings.
[0016] figure 1 is the contact schematic diagram of a single asperity, δ is the deformation amount of the top of the asperity, r' is the radius of the contact cross-sectional area of the asperity, r is the contact radius of the asperity, and R is the curvature radius of the asperity top.
[0017] Step (1) Calculation of actual contact area and contact load of combined surface
[0018] 1.1 Elastic deformation
[0019] When a'>a' c1 When the asperity deforms elastically, the actual contact area of a single asperity a ε , elastic contact load ΔF ε (a') and average contact pressure ΔP ε (a') can be expressed as
[0020] { ...
PUM
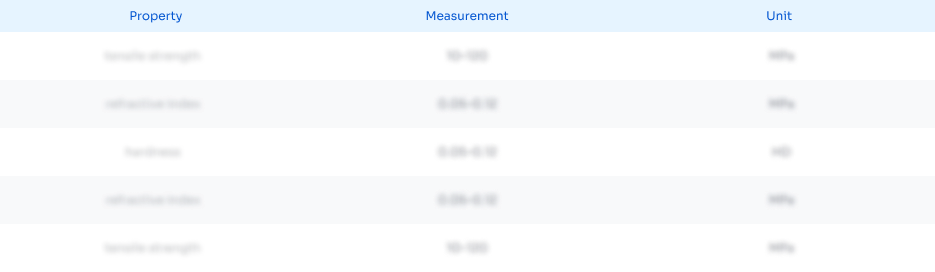
Abstract
Description
Claims
Application Information

- Generate Ideas
- Intellectual Property
- Life Sciences
- Materials
- Tech Scout
- Unparalleled Data Quality
- Higher Quality Content
- 60% Fewer Hallucinations
Browse by: Latest US Patents, China's latest patents, Technical Efficacy Thesaurus, Application Domain, Technology Topic, Popular Technical Reports.
© 2025 PatSnap. All rights reserved.Legal|Privacy policy|Modern Slavery Act Transparency Statement|Sitemap|About US| Contact US: help@patsnap.com