Hydraulic structure, and base seepage condition distributed optical fiber identification system and method thereof
A distributed optical fiber, hydraulic structure technology, applied in permeability/surface area analysis, testing of machine/structural components, testing of moving fluids/granular solids, etc. problems, to achieve the effect of improving engineering application capabilities, expanding application scope, and increasing monitoring distance
- Summary
- Abstract
- Description
- Claims
- Application Information
AI Technical Summary
Problems solved by technology
Method used
Image
Examples
Embodiment Construction
[0034] The present invention will be further described below in conjunction with the accompanying drawings.
[0035] Such as Figure 1 to Figure 3 As shown, a distributed optical fiber identification system for a hydraulic structure and its foundation seepage status of the present invention includes a special single-mode optical fiber 143 for self-control heat source seepage measurement that is vertically staggered in the hydraulic structure seepage monitoring area 130, and The optical path coupler 127 and the synchronous controller 102 connected by the special single-mode optical fiber 143 for the self-control heat source measurement are provided with a monitoring thermostatic chamber 129 between the special single-mode optical fiber 143 and the optical path coupler 127 for the self-control heat source measurement. The controller 102 sequentially communicates with the mode-locked laser 103, the first wavelength division multiplexer 104, the polarization beam splitter 105, the...
PUM
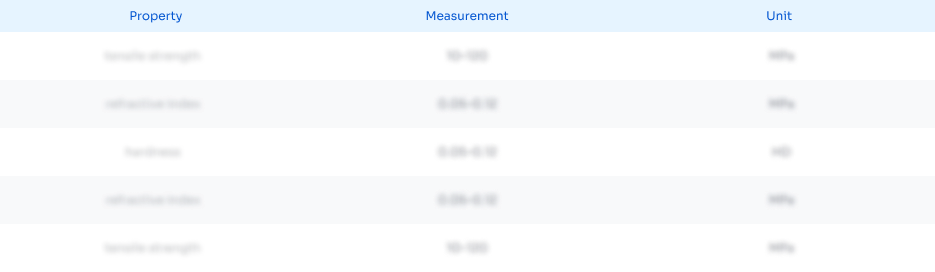
Abstract
Description
Claims
Application Information

- Generate Ideas
- Intellectual Property
- Life Sciences
- Materials
- Tech Scout
- Unparalleled Data Quality
- Higher Quality Content
- 60% Fewer Hallucinations
Browse by: Latest US Patents, China's latest patents, Technical Efficacy Thesaurus, Application Domain, Technology Topic, Popular Technical Reports.
© 2025 PatSnap. All rights reserved.Legal|Privacy policy|Modern Slavery Act Transparency Statement|Sitemap|About US| Contact US: help@patsnap.com