A non-copolymerized silicone oil modified polyether polymer water-repellent finishing agent and its preparation method
A technology of water-repellent finishing and finishing agent, which is applied in the field of finishing agent and its preparation, and the preparation of non-copolymerized silicone oil modified polyether polymer water-repellent finishing agent. problems, to achieve good soft smoothness and stable performance
- Summary
- Abstract
- Description
- Claims
- Application Information
AI Technical Summary
Problems solved by technology
Method used
Image
Examples
preparation example Construction
[0015] A method for preparing a non-copolymerized silicone oil-modified polyether water-repellent finishing agent, the steps are as follows:
[0016] 1) Synthesis of epoxy-terminated polyether: In a four-necked reaction bottle, add multifunctional polyether compound, heat to 60-90°C, according to the amount of substance, multifunctional polyether compound: tetrabutyl bromide Ammonium chloride: NaOH: epichlorohydrin = 1: 0.01-0.03: 1.5-3.5: 2-3.5 is added to the reaction flask, the epichlorohydrin is added dropwise for 30-60 minutes, stirred evenly, and the vacuum degree is -0.09 Mpa under reduced pressure distillation sloughs unreacted matter, obtains light yellow opaque solid and is epoxy-terminated polyether;
[0017] 2) Synthesis of amino silicone oil: In a four-necked flask connected with a vacuum distillation device, add octamethylcyclotetrasiloxane, a coupling agent, and a catalyst, and synthesize a macromolecular amino through three-stage heating and decompression. sil...
Embodiment 1
[0024] 1) Add 185.34g of multifunctional polyether compound into a 500ml four-necked reaction flask, melt it completely at 75°C, add 0.33g of tetrabutylammonium bromide, 1.5g of solid NaOH, and 3.75g of liquid 40%wtNaOH, and weigh 11.56g of epichlorohydrin was added dropwise to the reaction system in 30-60min, after the dropwise addition was completed, the reaction was carried out at constant temperature for 1.5h, and a light yellow opaque solid was collected;
[0025] 2) Add 300g of octamethylcyclotetrasiloxane, 33.7g of coupling agent, and 0.2g of catalyst into the reaction flask connected with vacuum distillation, keep the temperature at 95°C for 2h under the pressure of -0.035~0.04Mpa, and continue to depressurize To -0.06~-0.07Mpa, continue to keep constant temperature for 2 hours, raise the vacuum degree to -0.095Mpa, raise the temperature to 153°C, hold the pressure for 2h, cool down to 80°C and discharge, the transparent liquid is amino silicone oil, and the measured am...
Embodiment 2
[0028] 1) Add multifunctional 185.34g into a 500ml four-necked reaction flask, melt it completely at 75°C, add 0.48g of tetrabutylammonium bromide, 1.5g of solid NaOH, 3.75g of liquid 40%wtNaOH, and weigh epichlorohydrin 13.88g was added dropwise to the reaction system in 30-60min. After the dropwise addition, the constant temperature reaction was carried out for 1.5 hours, and a light yellow opaque solid was collected;
[0029] 2) Add 300g of octamethylcyclotetrasiloxane, 33.7g of coupling agent, and 0.2g of catalyst wq into the reaction flask connected with vacuum distillation. Press down to -0.06~-0.07Mpa, keep constant temperature for 2h, increase the vacuum degree to -0.095Mpa, raise the temperature to 153°C, hold the pressure for 2h, cool down to 80°C and discharge, the transparent liquid is amino silicone oil, the measured amine value is 0.61, the molecular weight determined by viscosity method is 5404;
[0030] 3) Add 242.4g of the solid obtained in step 1) and 200g ...
PUM
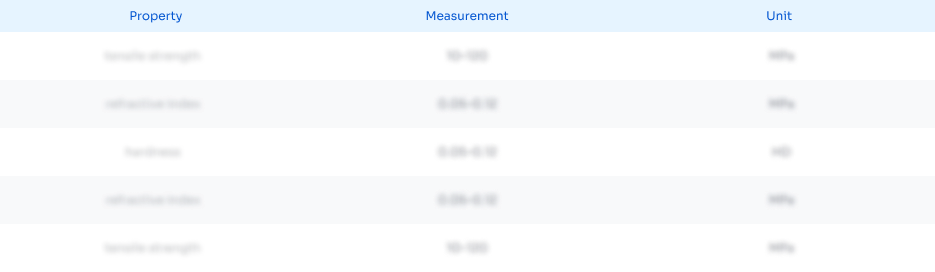
Abstract
Description
Claims
Application Information

- Generate Ideas
- Intellectual Property
- Life Sciences
- Materials
- Tech Scout
- Unparalleled Data Quality
- Higher Quality Content
- 60% Fewer Hallucinations
Browse by: Latest US Patents, China's latest patents, Technical Efficacy Thesaurus, Application Domain, Technology Topic, Popular Technical Reports.
© 2025 PatSnap. All rights reserved.Legal|Privacy policy|Modern Slavery Act Transparency Statement|Sitemap|About US| Contact US: help@patsnap.com