Control method for inclusions in heavy rail steel
A control method and inclusion technology, applied in the manufacture of converters, etc., can solve the problems of low desulfurization efficiency and no consideration of inclusions, etc., and achieve high desulfurization efficiency, desulfurization efficiency and stable effects
- Summary
- Abstract
- Description
- Claims
- Application Information
AI Technical Summary
Problems solved by technology
Method used
Examples
Embodiment 1
[0049] A, converter smelting
[0050] The molten iron entering the converter has a S content of 0.016%. After the converter smelting is finished, tapping begins. During the tapping process, a silicon-calcium-barium alloy is added to the ladle for deoxidation. The addition amount is 2.5kg silicon-calcium-barium and silicon-calcium per ton of molten steel. After the addition of barium is completed, other alloys required for the steel type are added immediately. When the tapping volume is 90 tons, adding active lime to the ladle is 5kg per ton of molten steel. After tapping, add calcium carbide evenly to the slag surface of the ladle to add 0.2kg per ton of molten steel. In the above-mentioned tapping process, the flow rate of argon blowing at the bottom of the ladle is 60 NL / min. After tapping, the bottom argon flow rate of 50NL / min is used to blow argon for 6 minutes, and then the molten steel is sent to LF for refining.
[0051] B, LF furnace refining
[0052] After the molten st...
Embodiment 2
[0059] A, converter smelting
[0060] The molten iron entering the converter has a S content of 0.020%. After the converter smelting is completed, tapping begins. During the tapping process, a silicon-calcium-barium alloy is added to the ladle for deoxidation. The addition amount is 3.5kg silicon-calcium-barium and silicon-calcium-barium per ton of molten steel. After the addition is complete, add other alloys required by the steel grade. When the tapping volume is 90 tons, 5kg of active lime per ton of molten steel is added to the ladle. After tapping, 0.4kg of calcium carbide per ton of molten steel is evenly added to the slag surface of the ladle. In the above-mentioned tapping process, the flow rate of argon blowing at the bottom of the ladle is 60 NL / min. After tapping, the bottom argon flow rate of 50NL / min is used to blow argon for 6 minutes, and then the molten steel is sent to LF for refining.
[0061] B, LF furnace refining
[0062] After the molten steel arrives at the...
Embodiment 3
[0069] A, converter smelting
[0070] The molten iron entering the converter has a S content of 0.010%. After the converter smelting is finished, tapping begins. During the tapping process, a silicon-calcium-barium alloy is added to the ladle for deoxidation. The addition amount is 3.0kg per ton of molten steel. After the silicon-calcium-barium addition is complete Immediately add other alloys required by the steel grade. When the tapping volume is 90 tons, 3kg of active lime per ton of molten steel is added to the ladle. After tapping, add 0.3kg of calcium carbide per ton of molten steel evenly to the slag surface of the ladle. In the above-mentioned tapping process, the flow rate of argon blowing at the bottom of the ladle is 60 NL / min. After tapping, the bottom argon flow rate of 50NL / min is used to blow argon for 6 minutes, and then the molten steel is sent to LF for refining.
[0071] B, LF furnace refining
[0072] After the molten steel arrives at the LF station, turn on t...
PUM
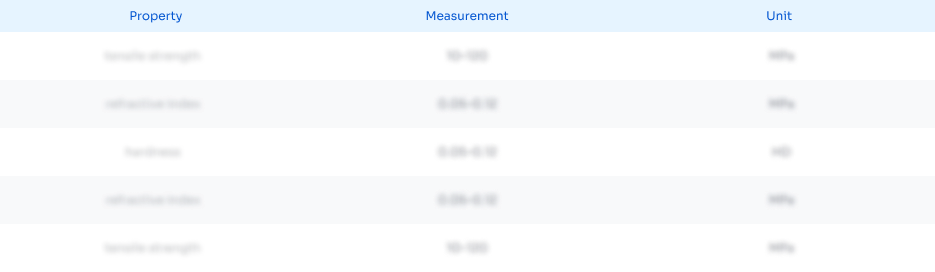
Abstract
Description
Claims
Application Information

- Generate Ideas
- Intellectual Property
- Life Sciences
- Materials
- Tech Scout
- Unparalleled Data Quality
- Higher Quality Content
- 60% Fewer Hallucinations
Browse by: Latest US Patents, China's latest patents, Technical Efficacy Thesaurus, Application Domain, Technology Topic, Popular Technical Reports.
© 2025 PatSnap. All rights reserved.Legal|Privacy policy|Modern Slavery Act Transparency Statement|Sitemap|About US| Contact US: help@patsnap.com