Multilateral mould of site precast concrete pile and manufacturing method of precast concrete pile
A technology of prefabricated concrete and production methods, which is applied in the direction of molds, manufacturing tools, mold trays, etc., can solve the problems of long maintenance period, high construction cost, and increased cost, and achieve the effects of reducing transportation links, improving work efficiency, and reducing production costs
- Summary
- Abstract
- Description
- Claims
- Application Information
AI Technical Summary
Problems solved by technology
Method used
Image
Examples
Embodiment Construction
[0037] figure 1 It is a schematic cross-sectional view of an embodiment of the bottom template in the polygonal mold of the prefabricated concrete pile of the present invention, as figure 1 As shown, the bottom template 1 is made of concave channel steel, the notch of the concave channel steel faces downward, and its top surface constitutes the bottom edge of the polygonal mold.
[0038] figure 2 It is a schematic cross-sectional view of an embodiment of the monolithic formwork in the side formwork in the polygonal mold of the present invention, image 3 It is a side view of an embodiment of the monolithic formwork in the side formwork in the polygonal mold of the present invention, as figure 2 and image 3 As shown, the single formwork 3 is pressed into a triangular shape with the same bending angle and the same edge distance by steel plate, the edge distance of the single formwork 3 is similar to the width of the bottom formwork 1, and the outer edge of the single formw...
PUM
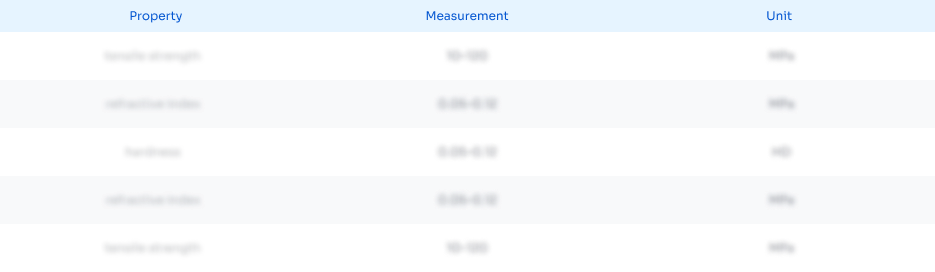
Abstract
Description
Claims
Application Information

- R&D
- Intellectual Property
- Life Sciences
- Materials
- Tech Scout
- Unparalleled Data Quality
- Higher Quality Content
- 60% Fewer Hallucinations
Browse by: Latest US Patents, China's latest patents, Technical Efficacy Thesaurus, Application Domain, Technology Topic, Popular Technical Reports.
© 2025 PatSnap. All rights reserved.Legal|Privacy policy|Modern Slavery Act Transparency Statement|Sitemap|About US| Contact US: help@patsnap.com