A high-pressure combustion chamber cooling jacket inlet and outlet structure and its processing method
A processing method and combustion chamber technology, applied in the aerospace field, can solve the problems of channel structure deformation, large local flow resistance, and difficulty in removing excess burrs, and achieve the effects of improving work performance, ensuring uniformity, and avoiding burrs.
- Summary
- Abstract
- Description
- Claims
- Application Information
AI Technical Summary
Problems solved by technology
Method used
Image
Examples
Embodiment Construction
[0032] The present invention will be described in further detail below in conjunction with the accompanying drawings and specific embodiments.
[0033] Such as Figure 5 and Image 6 As shown, the inlet and outlet structure of the cooling jacket of the high-pressure combustor includes a cylindrical combustor inner wall 3 and a combustor outer wall 2 . An interlayer channel 4 is formed between the inner and outer walls, and the space in the combustion inner wall 3 forms a combustion chamber 5 . The connecting ribs 7 are formed by milling grooves on the combustion inner wall 3 . The outer wall of the combustion chamber 2 is connected to the connecting ribs 7 of the inner wall of the combustion chamber 3 by high-strength metal formed by electroforming or diffusion welding, and the gap between the connecting ribs 7 is the interlayer channel 4 .
[0034] Different from the prior art, the formation of the interlayer channel inlet 1 and the interlayer channel outlet 6 of the prese...
PUM
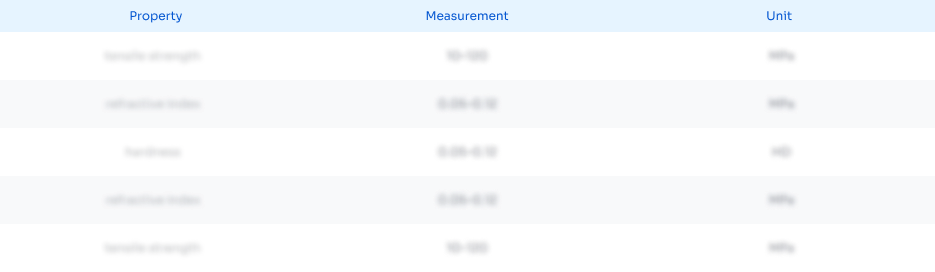
Abstract
Description
Claims
Application Information

- R&D
- Intellectual Property
- Life Sciences
- Materials
- Tech Scout
- Unparalleled Data Quality
- Higher Quality Content
- 60% Fewer Hallucinations
Browse by: Latest US Patents, China's latest patents, Technical Efficacy Thesaurus, Application Domain, Technology Topic, Popular Technical Reports.
© 2025 PatSnap. All rights reserved.Legal|Privacy policy|Modern Slavery Act Transparency Statement|Sitemap|About US| Contact US: help@patsnap.com