Ceramic controllable fambe glaze
A technology for kiln changing glaze and glaze, applied in the field of glaze, can solve the problems of complicated process, time-consuming and laborious, high production cost, and achieve the effects of improving production efficiency, reducing production cost and simplifying the firing process
- Summary
- Abstract
- Description
- Claims
- Application Information
AI Technical Summary
Problems solved by technology
Method used
Examples
Embodiment 1
[0044] The glaze material used for the ice-cracking bottom material is prepared by the following raw materials according to the number of parts:
[0045] Albite 50 parts
[0046] Spodumene 10 parts
[0047] 28 parts of boric acid
[0048] Quartz 20 parts
[0049] Double Fly 18 copies
[0050] When making, feldspar, quartz, and boric acid are melted into a frit at a high temperature of 1300°~1400°, and then spodumene and Shuangfei are ball milled together for about 10 hours and dried to form a finished product for use.
[0051] During the printing operation, the part of the designed decal paper that needs to be ice-cracked can be printed once with a screen (80-200 mesh) using the above-mentioned raw materials as needed. If a certain color is required for the cracked part of the ice, the pigment (0.5~10% depending on the color depth) can be added to the above primer, and then printed according to the above operation. If the desired color is red, after the above operations, ...
Embodiment 2
[0069] In the present embodiment, the glaze material used for the ice-cracking base material is prepared by the following raw materials according to the number of parts:
[0070] Albite 30 parts
[0071] Spodumene 5 parts
[0072] 14 parts boric acid
[0073] Quartz 8 parts
[0074] Double Fly 5 copies
[0075] Its manufacturing method is identical with embodiment one with printing operation.
[0076] The glaze material used in the crystal base material is formulated by the following raw materials according to the number of parts:
[0077] 50 parts of quartz sand
[0078] 6 parts cryolite
[0079] 10 parts of anhydrous soda ash
[0080] chalk 1 part
[0081] 2 parts saltpeter;
[0082] Its manufacturing method is identical with embodiment one with printing operation.
[0083] The glaze material used for the rhytogenic bottom material is formulated by the following raw materials according to the number of parts:
[0084] Feldspar 20 parts
[0085] Quartz 5 parts
...
Embodiment 3
[0091] In the present embodiment, the glaze material used for the ice-cracking base material is prepared by the following raw materials according to the number of parts:
[0092] Albite 70 parts
[0093] Spodumene 20 parts
[0094] 35 parts boric acid
[0095] Quartz 40 parts
[0096] Double Fly 5 copies
[0097] Its manufacturing method is identical with embodiment one with printing operation.
[0098] The glaze material used in the crystal base material is formulated by the following raw materials according to the number of parts:
[0099] 150 parts of quartz sand
[0100] 30 parts of cryolite
[0101] 50 parts of anhydrous soda ash
[0102] Chalk 10 parts
[0103] 15 parts of saltpeter;
[0104] Its manufacturing method is identical with embodiment one with printing operation.
[0105] The glaze material used for the rhytogenic bottom material is formulated by the following raw materials according to the number of parts:
[0106] Feldspar 70 parts
[0107]Quartz...
PUM
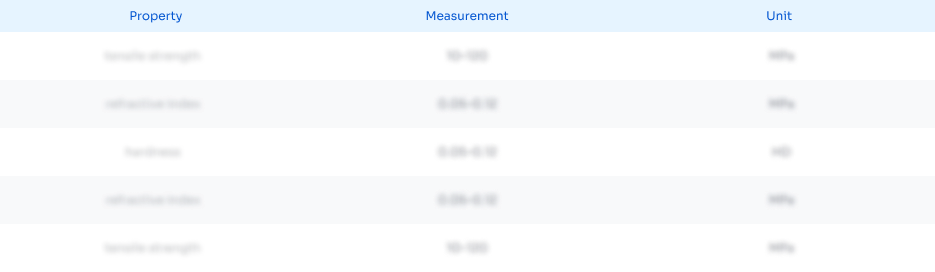
Abstract
Description
Claims
Application Information

- R&D
- Intellectual Property
- Life Sciences
- Materials
- Tech Scout
- Unparalleled Data Quality
- Higher Quality Content
- 60% Fewer Hallucinations
Browse by: Latest US Patents, China's latest patents, Technical Efficacy Thesaurus, Application Domain, Technology Topic, Popular Technical Reports.
© 2025 PatSnap. All rights reserved.Legal|Privacy policy|Modern Slavery Act Transparency Statement|Sitemap|About US| Contact US: help@patsnap.com